- Without proper component preparation, resulting welds may be of poor quality, leak or fail in the field.
- Porosity, or bubble formation, can be avoided by thoroughly cleaning components and making sure surfaces are dirt free.
- Industrial cleaning wipes can remove any trace of cutting fluids, grime, oils, inks, or grease.
Welding is a common industrial fusion process that permanently joins metal components together. It has been used, in its modern form, for well over 100 years. Though techniques, equipment and materials have improved every year and greatly increased welding efficiency, one thing remains relatively unchanged: the importance of component preparation. If this first step is skipped, or performed with inappropriate techniques, the resultant welds may be of poor quality, and could leak or fail catastrophically in the field.
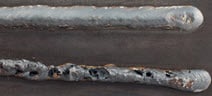
Porosity is one of the most common weld quality issues, and it is generally caused by the inadvertent addition of an impurity into the weld puddle. In a weld joint, porosity is essentially a “bubble formation” created by gas trapped in the molten metal. Any grease, oil, dirt or moisture content introduced into the weld zone can contribute to the porosity.
To reduce the possibility of contamination, and to ensure a high-quality weld, follow these best practices:
- Thoroughly clean the components prior to welding. Wipe down the surfaces to be welded with a shop cloth saturated with a liquid solvent.
- Make sure that surfaces in the welding area are dirt free. Strong breezes from shop fans or openings to the outdoors can blow contaminants into the weld puddle.
To ensure the removal of any trace of cutting fluids, grime, oils, inks, or grease, Keller Technology Corporation uses a relatively new product, produced by the Aquasol Corporation that was specifically engineered for this cleaning process.
EZ Wipes Industrial Cleaning Wipes are two-sided, shred-resistant wipes saturated with a concentrated, eco-friendly, cleaning solution. These single-use wipes reduce the likelihood of cross contamination and are a safer alternative to volatile solvents. They are also easily disposed of since they do not require any special hazardous waste handling or containers.
Though there are many other important steps when it comes to producing a high quality weld, proper component preparation will improve the opportunity for great results. Porosity, one of the most common weld quality issues, can be significantly reduced by diligently following industry standard weld process control and component cleaning procedures. Contact Keller Technology for more information on our extensive welding, machining and inspection capabilities.