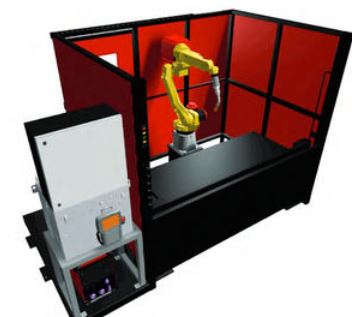
- KTC’s fabrication department features a Lincoln Electric Automate Welding Cell.
- The cell welds carbon steel, aluminum and stainless steel alloys.
- The welding cell also processes vacuum chambers, pressure vessels and complex fabrications.
Keller Technology Corporation’s (KTC) continued investment in new manufacturing equipment allows us to offer our customers the latest technology, helping them to stay competitive in their respective high-tech industries. A highlight of our fabrication department is a Lincoln Electric Automated Welding Cell used to weld carbon steel, aluminum and stainless steel alloys.
Utilizing a robotic arm and controller from Fanuc America Inc., the state-of-the-art system from Lincoln Electric Company processes vacuum chambers, pressure vessels and complex fabrications in KTC’s Tonawanda, NY, facility. Robotic welding systems are more affordable and easier to operate and program than ever before. With these recent improvements, more short- to medium-run applications and specialized projects can now justify automation.
Other reasons for making the move to automate a portion of product volume include:
- Suitability for Large Parts – A robotic welding system is ideal for large parts requiring multiple reorientations during the welding process.
- Consistent Quality – With fewer uncontrolled variables in the process, higher quality welds and more uniform results were quickly realized. This reduced post-weld processing and rework, resulting in faster turnaround times and increased throughput.
- Skilled Worker Shortage – As with many trades, there is currently a severe shortage of skilled welders in many regions of the country. This reality creates an environment where it made sense to transfer the knowledge of our skilled master craftsman to the machine and automate as many of his or her repetitive tasks as possible. Our welders are still intimately involved in the process, working on tasks not suitable for the robotic cell; however, the overall labor content of the product is lower and throughput in the weld shop has increased.
Fabricated parts that require many hours of tedious welding, hand-held grinding and polishing may represent a significant percentage of the cost of a complex system or machine.
If you have a contract manufacturing or automation project requiring multiple complex fabrications, and you’re wondering if robotic welding could lower your costs, contact us today and we will be happy to assist you with your decision.