Sourcing Large-Format 5-Axis Machining
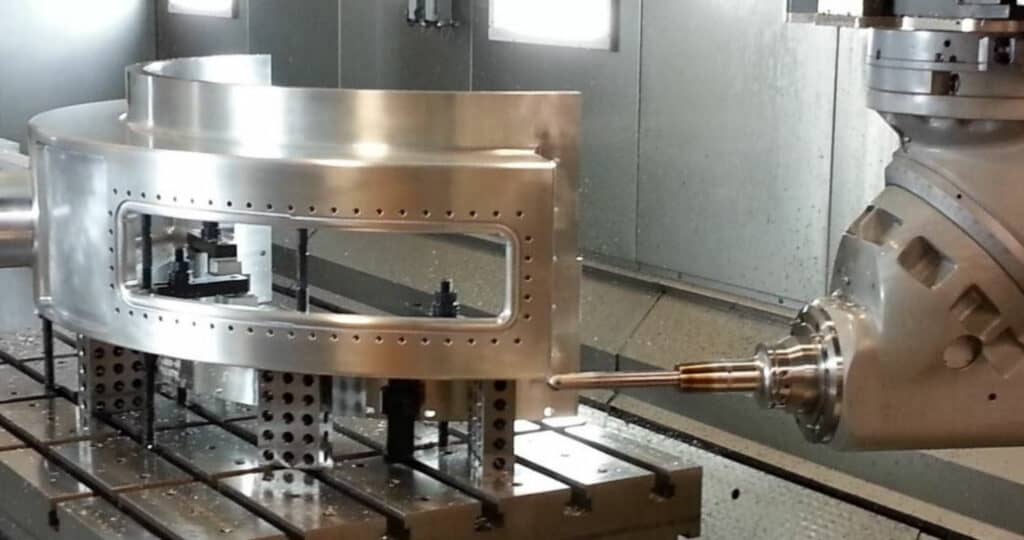
If you have ever tried sourcing large, tight-tolerance machined components, you already know: the larger and more complex the part, the smaller the vendor list. When the part requires 5-axis machining, tight tolerances, and certified welding, the challenge only multiplies. Why is it so hard to find a shop that can manage it all? And […]
Supporting Fusion Energy Through Machining and Precision Fabrication
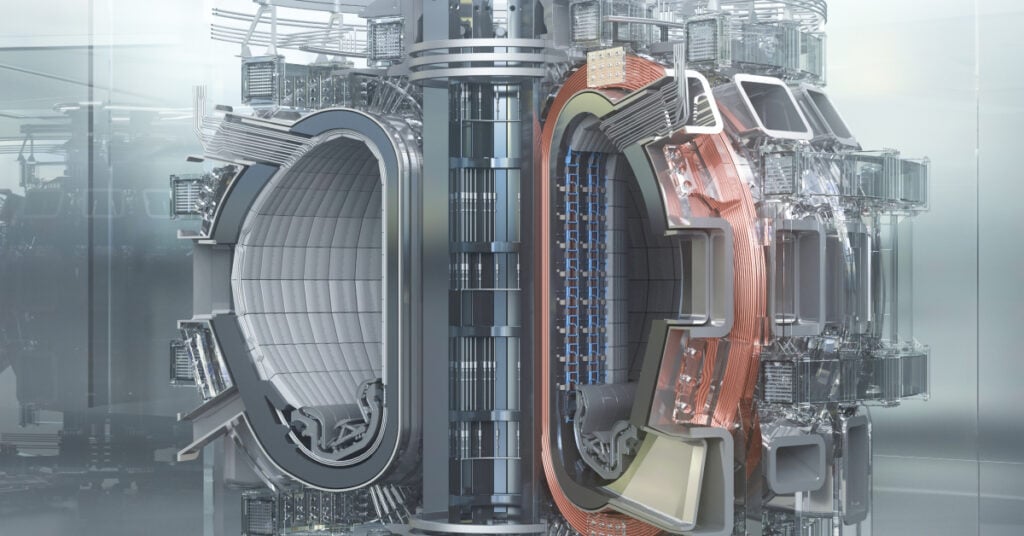
Fusion energy, long regarded as the “holy grail” of clean energy, is on the brink of becoming a transformative reality. With global investments surging into the development of several different approaches to achieving fusion, advanced fusion energy machines and reactors, the demand for specialized machining and fabrication expertise has never been greater. At Keller Technology […]
State-of-the-Art 5-Axis Machine Tools for Large, Precision Components
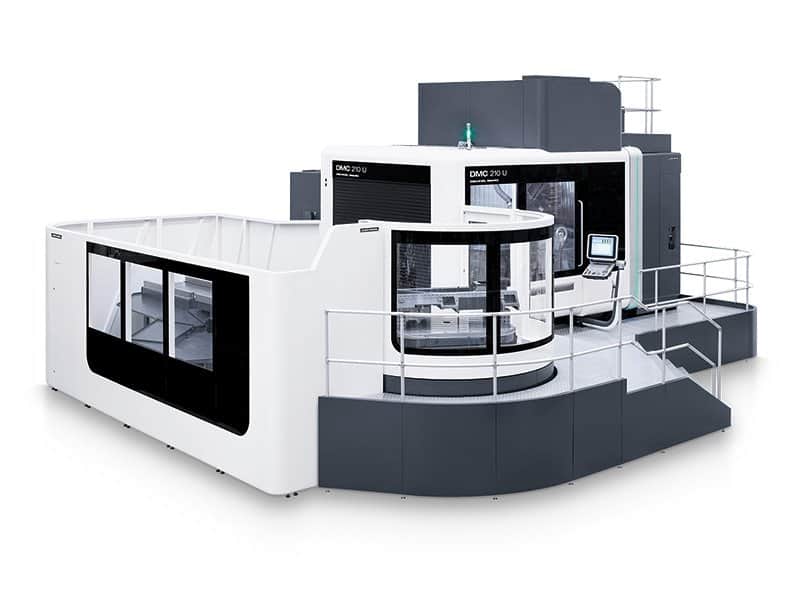
In the world of manufacturing, precision and innovation go hand in hand. As industries like aerospace, energy, medical, and semiconductor manufacturing demand increasingly complex and high-performance components, staying ahead requires more than just expertise—it demands continuous investment in advanced technologies. Among the most transformative advancements in machining are state-of-the-art 5-axis machine tools, which are revolutionizing […]
5 Innovations in Industrial Robotics and Automation
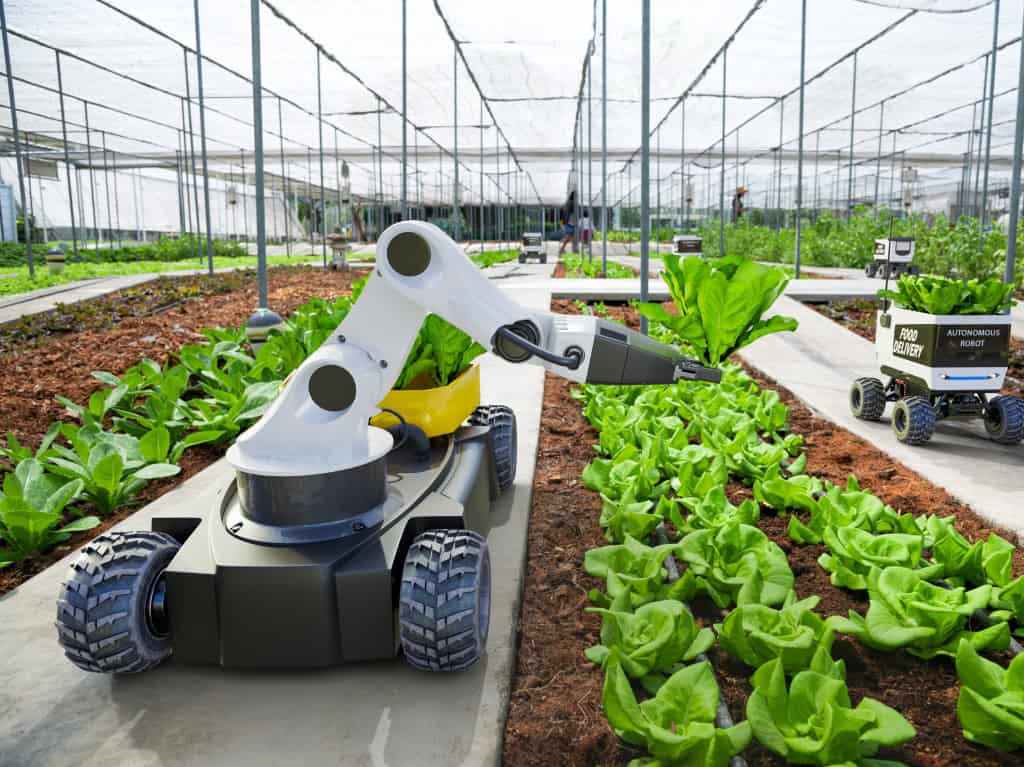
Explore the Latest Innovations Changing the Game Collaborative Robots (Cobots): Transforming the Workforce Collaborative robots, or cobots, are one of the most significant innovations in industrial robotics. Unlike traditional robots that operate in a guarded environment, segregated from humans, cobots are designed to work alongside humans, enhancing workplace safety and productivity. Equipped with advanced sensors, […]
Case Study: Automating the Design of a High-Precision Opto-mechanical Assembly
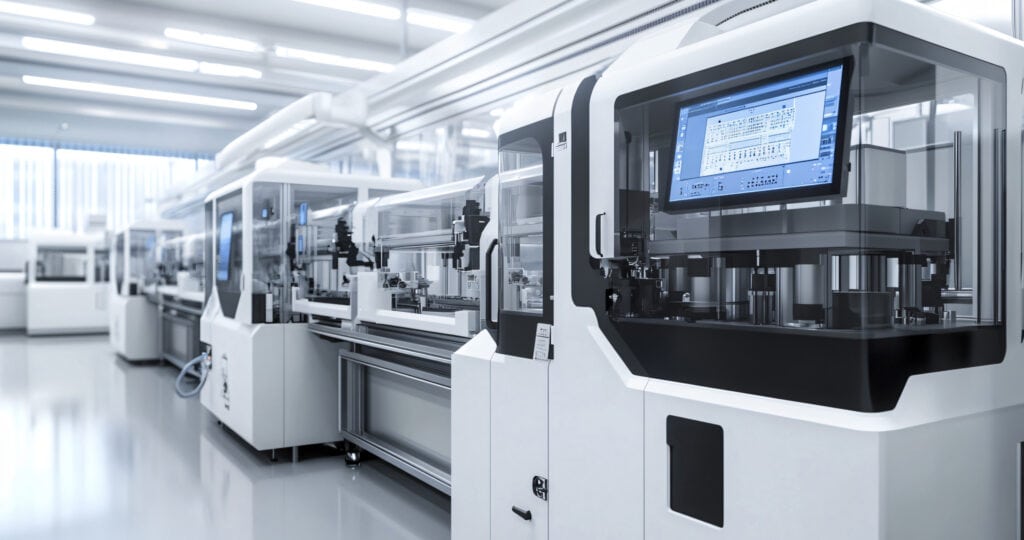
Summary This case study details Keller Technology Corporation’s (KTC) successful development of a custom automated system for assembling a high-precision opto-mechanical assembly. The customer, facing challenges with scaling a manual assembly operation, sought to improve production throughput, reduce defects, and enhance quality control. Through a structured proof-of-concept approach, KTC validated the feasibility of automation and […]
Precision Machining and Fabrication in the Emerging Small Modular Reactor Industry
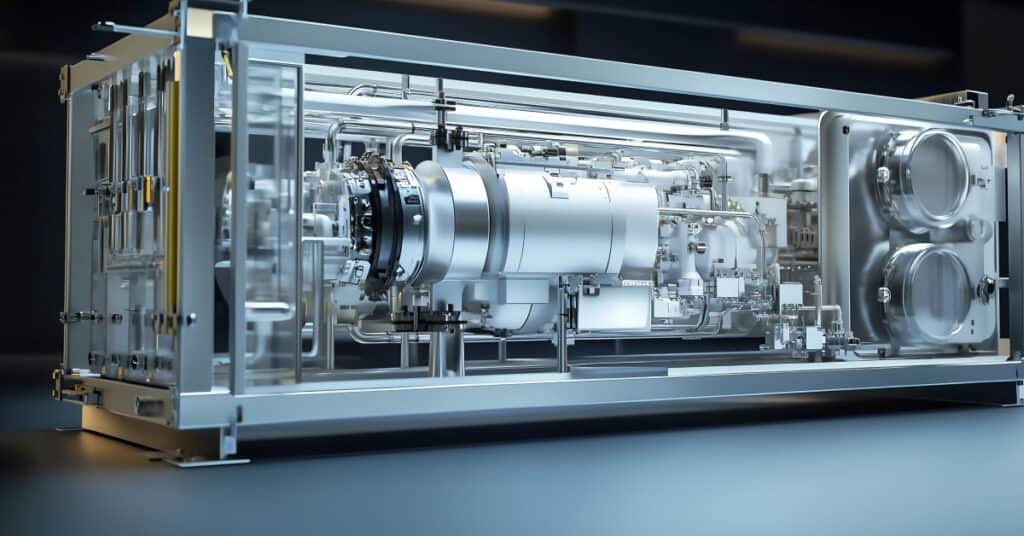
As the global push for clean, reliable energy intensifies, Small Modular Reactors (SMRs) are emerging as a game-changing solution in the nuclear power sector. Designed to be smaller, safer, and more flexible than traditional nuclear reactors, SMRs promise to revolutionize how nuclear power is deployed and scaled. Behind the scenes, precision machining and fabrication are […]