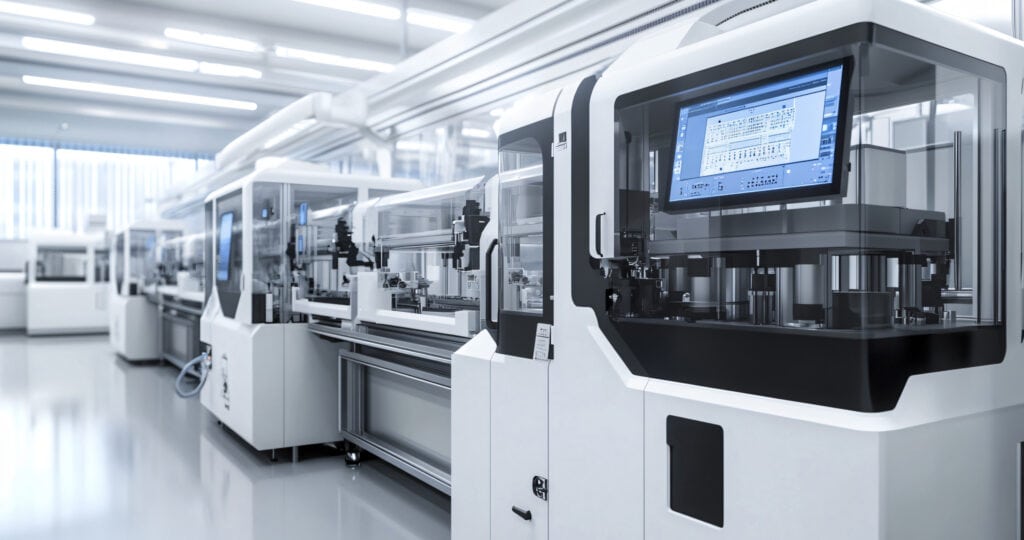
Summary
This case study details Keller Technology Corporation’s (KTC) successful development of a custom automated system for assembling a high-precision opto-mechanical assembly. The customer, facing challenges with scaling a manual assembly operation, sought to improve production throughput, reduce defects, and enhance quality control. Through a structured proof-of-concept approach, KTC validated the feasibility of automation and vision inspection, leading to the design, build, and deployment of a fully automated production cell. The final system delivered improved efficiency, reduced rework costs, and a scalable solution for future production growth.
Background
The customer, a leading manufacturer of precision optical components, devices, and systems, relied on a manual assembly process for the insertion of optical lenses. While the existing process had moderate yields, defects were only detectable much later in the production workflow, making rework costly and inefficient. Seeking to improve cycle time, quality, and overall yield, the customer explored automation but had been unsuccessful in prior attempts with external machine builders. Recognizing the complexity of the task, they partnered with KTC to develop an automated solution.
Client Description
The client is a high-tech manufacturer specializing in precision optical systems used in advanced imaging and sensing applications. Their products require extreme precision in assembly and quality control, making automation a natural step toward improving consistency and reducing costly defects.
Project Goals and Objectives
The primary goal of this project was to automate the optical lens insertion process to improve efficiency, reduce defects, and enhance quality control through automated vision inspection. Specific objectives included:
- Feasibility Validation: Conducting a proof-of-concept to verify that automation could be successfully implemented.
- Process Improvement: Reducing rework costs by enabling real-time defect detection.
- Cycle Time Reduction: Increasing throughput with repeatable and reliable automation.
- Scalable Design: Ensuring the system could be adapted for future production needs.
Challenges Faced
Technical Challenges
- Precision Requirements: The placement tolerances for optical lenses were extremely tight, requiring advanced robotic and vision-based alignment techniques.
- Vision Inspection Complexity: The system needed to detect defects in real time to prevent defective assemblies from progressing further down the production line.
- Automated Handling of Delicate Components: Opto-mechanical assemblies are highly sensitive, necessitating careful handling to prevent damage during automation.
Operational Challenges
- Customer’s Prior Automation Integrator Difficulties: The customer had attempted automation externally without success, making it critical to demonstrate proof-of-concept validation before full-scale development.
- Integration with Existing Production Workflows: The new system needed to seamlessly integrate into the customer’s manufacturing process while improving efficiency.
- Knowledge Transfer and Training: Ensuring the customer’s engineering and operations teams were fully trained on the new system was essential for long-term success.
Results and Outcomes
The project followed a structured approach, ensuring a successful outcome:
Proof-of-Concept Validation:
- KTC worked with the customer to develop a prototype that confirmed automation feasibility.
- The opto-mechanical assembly prototype successfully demonstrated that vision inspection could detect defects and that robotic handling could achieve the required precision.
Custom System Development:
- KTC collaborated with the customer to define and finalize requirements for the automated production cell.
- KTC engineers designed, programmed, and fully tested the system, ensuring it met all performance and quality requirements.
Factory Acceptance Test (FAT) and Installation:
- The customer’s engineering and operations teams performed a FAT at KTC’s facility, validating the system’s performance.
- KTC engineers accompanied the machine for on-site installation, assisted with SAT, and provided hands-on training for operators and maintenance personnel.
Operational Improvements:
- The automated system successfully increased production throughput and reduced cycle times.
- Real-time vision inspection prevented defective parts from moving downstream, significantly lowering rework costs.
- The system provided consistent, repeatable results, ensuring long-term reliability and scalability.
Lessons Learned
Key insights gained from this project include:
- Early Proof-of-Concept Reduces Risk: Conducting feasibility testing before full-scale development helps mitigate project risks and ensures a successful outcome.
- Close Collaboration Drives Success: Regular engagement with the customer throughout design and testing ensures the final system meets real-world production needs.
- Vision Systems Enhance Quality Control: Implementing automated inspection at the assembly stage prevents costly downstream rework and improves overall yield.
- Training and Support Ensure Long-Term Success: On-site installation, testing, and training empower the customer’s team to operate and maintain the system effectively.
These lessons reinforce KTC’s commitment to delivering innovative automation solutions tailored to the unique needs of each client.
Client Satisfaction
The customer expressed high satisfaction with KTC’s ability to execute a challenging automation project successfully. They highlighted the structured proof-of-concept approach, which minimized risk, and the comprehensive training and support provided during system deployment. The new system not only met but exceeded expectations in terms of quality, efficiency, and ease of use.
Conclusion
This project showcases KTC’s ability to develop and deploy highly specialized automation solutions for precision assembly applications. By leveraging engineering expertise, advanced robotics, and vision technology, KTC successfully delivered a reliable, scalable automation system that improved production efficiency and reduced costs. The success of this project further solidifies KTC’s role as a trusted partner for manufacturers seeking to implement automation in high-precision environments. Contact KTC for your next precision assembly project.