Material selection is crucial in all aspects of a vacuum system, especially when using precision fabrication equipment to build vacuum chambers. Vacuum chambers play a big role in precision fabrication where maintaining controlled environments is essential for processes. In a vacuum vessel, the walls must be strong enough to withstand the pressure difference of the system pressure and the external atmosphere. The vessel material in a vacuum system must be able to be joined to other materials to create valves, flanges and feedthroughs. Still other materials must be used to create leak-tight seals at connection points for system components.
In general, materials in a vacuum system need:
- Wide temperature tolerance
- Similar thermal expansion rates
- Low outgassing rate
Other potentially desirable traits include:
- High strength
- Elasticity
- Electrical conduction or insulation
- Thermal conduction or insulation
- Non-magnetic
- Low volatility
- Low chemical reactivity
- Radiation resistance
In metals selection, machinability, leak-tightness of welded or brazed joints and corrosion resistance are important considerations. The pressure range is also a factor when selecting metals for vessel walls.
- For ultra-high vacuum, the density and purity of melted and cast materials is highly useful, however it’s also relatively expensive.
- In high-vacuum systems, drawn, rolled and pressed materials work well, but be aware they may exhibit leaks in the rolling direction.
- Cast materials are cost-effective and suitable in fine and coarse vacuum systems.
Manufacturing Vacuum Systems
Different Materials Used in Vacuum System Design and Fabrication
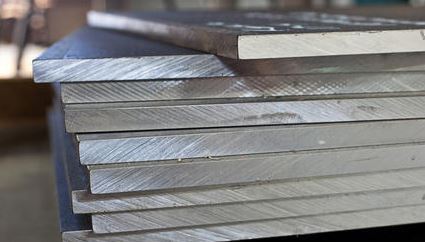
Stainless Steel
(Particularly 304 SST) widely used for vacuum vessels and vacuum chambers in precision fabrication – high-strength, suitable for wide temperature changes, doesn’t easily oxidize and may be joined by welding or brazing.
Copper
(Particularly OFHC – oxygen-free, high conductivity) commonly used for gasket seals and feedthroughs – doesn’t outgas much, withstands wide temperature changes, excellent conductor of electricity and heat, may be joined by welding or brazing, relatively soft with few microscopic leak paths and may be nickel-plated to improve its chemical resistance.
Ceramics
Excellent insulator for electricity and heat, fragile but has great compressive strength, low thermal expansion rate and may be brazed to other materials in the system.
Kovar
Magnetic alloy composed of 54 percent iron, 29 percent nickel, and 17 percent cobalt – intermediate material used to join glass-to-metal or ceramic-to-metal through brazing. Coefficient of expansion is between that of ceramics and stainless steel and provides vacuum-tight seal between materials even in extreme temperatures.
Elastomers
Commonly used for gasket seals – flexible but not compressible, soft, high elasticity (and therefore reusable), permeability may make them unsuitable for UHV systems, generally permeable to helium, which can complicate leak testing. Specific examples:
- Buna-N: synthetic rubber that’s inexpensive, resistant to helium, and useful in applications that are not heated about 80 C.
- Viton: widely used for O-rings, valve seal, and gaskets in temperatures up to 150 C. Low outgassing makes it suitable for both high and ultrahigh vacuum systems.
- Polyimide: a substitute for Viton in slightly higher temperature applications (up to 200 C). Requires more sealing pressure than other elastomers,] but is also more resistant to radiation. Absorbs water.
- Silicone: Useful in vacuum furnace applications. Silicone compounds are able to withstand high temperatures but have poor outgassing rates and are permeable to helium and water.
Contact us today to discuss our custom vacuum chamber capabilities. Keller is here to take care of all your custom precision fabrication, and vacuum system questions.