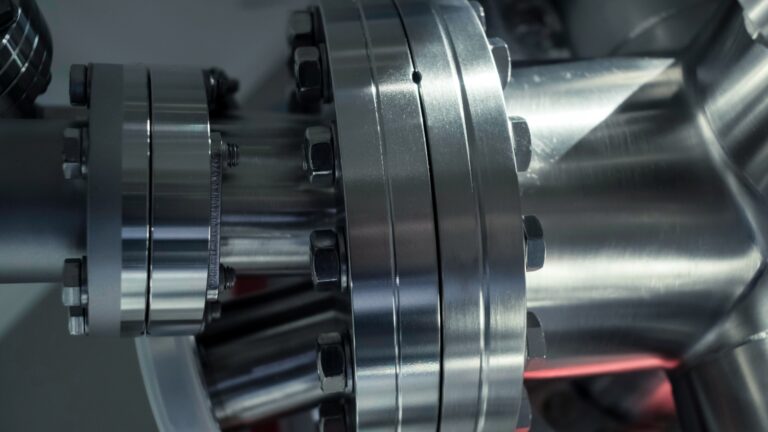
Achieving the ultimate pressure of a vacuum system is greatly affected by the amount of gases or vapors contained within the system. To improve initial pumping efficiency following assembly or maintenance activities, outgassing can be reduced by properly pretreating the components within the system. The higher the ultimate pressure specification, the greater the need for cleanliness, however all systems will benefit from proper pretreatment.
Prep the physical surface
In vacuum systems, surface porosity is an excellent trap for gases and vapors. The first pretreatment step involves smoothing that surface to remove thick oxide layers such as rust or aluminum oxide. The most effective means of removing surface porosity is by mechanical grinding, brushing, or blasting with glass or ceramic beads.
Clean to reduce surface contaminants
Once the physical surface is prepared, the next step is to reduce hydrocarbon contamination from oils and coolants that may have been introduced via machining, contamination from pumps or improper handling.
- Choose a soap or organic solvent that is compatible with the material
- Decide if the cleaning agent needs to be at an elevated temperature to increase its chemical activity
- Apply sufficient mechanical force (i.e. ultrasonic bath or high-pressure sprayer)
- Determine how much time the component will need to be exposed to the cleaning solution (e.g. dipping will require more time than spraying)
Bake at the highest material-permitted temperature to remove adsorbed gases and vapors
After the surface contaminants have been removed and the cleaning agents thoroughly rinsed away, the final step in the pretreatment process is the bake-out. For components, this can often be conducted inside a vacuum furnace. Baking helps to remove water adsorption from the surface of the material. In general, the higher the furnace temperature, the faster the degassing.
Keep your system clean
- Always protect opened vacuum systems from atmospheric and human contamination
- Take care to choose packing materials that do not transfer oily substances to the vacuum components, such as aluminum foil or plastic sheets with a low outgassing rate
- During assembly, consider environmental and human factors to avoid introducing outgassing contaminants into the system
- Environmental considerations include factors such as humidity, dust particles, and oil mist/vapor
- Human factors include special clothing to prevent contamination from fingerprints, dander, hair and perspiration, as well as using clean tools made of stainless steel or aluminum
Taking appropriate steps to prevent contamination will reduce the need for cleaning, and ultimately help to achieve the desired base pressure more efficiently. Our dedicated engineering staff is well-versed in the proper manufacture of custom vacuum chambers, from assembly through final test and packaging protocol.
Contact Keller Technology today to find out more about our custom vacuum chamber solutions.