Deburring is the process of chamfering or rounding sharp corners formed on a metallic part during the machining process. Deburring can also remove the raised edges and small pieces of material that may remain attached to a workpiece after it has been machined by a cutting tool or grinding wheel. Finishing processes alter the surfaces of a workpiece to remove machining marks, scaling or pitting. Finishing can also enhance the appearance or function of the part and prepare it for subsequent coating processes such as bonding, plating or painting. Deburring and finishing are important process steps that should not be overlooked by the engineers and technicians designing and manufacturing component parts.
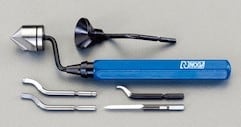
Hand Grinding, Sanding, Lapping and Polishing
Manual processing of parts is still commonplace in today’s modern manufacturing facilities. Many parts that are machined on sophisticated CNC equipment are still deburred and finished using an array of hand, ultrasonic and air powered tools. Files, stones, knives, abrasive sheets/compounds, and specialized deburring tools are utilized by the machinist or tool maker to complete the fabrication process based on the part’s geometry and the requirements communicated by the engineering drawing. Tedious and time-consuming hand work can add significant cost to a part; therefore if many identical parts are being produced, an automated deburring and finishing process is usually specified if possible.
Mass Finishing
Mass Finishing is a timed batch process that utilizes abrasive media and a rotating or vibrating process vessel to simultaneously deburr and finish multiple machined parts. These machines process any surface that comes in contact with the media. Ranging in size from small table top units used for processing rings and other jewelry to massive rectangular tub machines twenty feet long used for finishing aluminum aircraft parts. The processing vessels are generally fitted with a tough rubber liner to protect them from the media and prevent damage to the parts being processed. There are countless combinations of media sizes, shapes and materials which are selected based on the machined part’s physical characteristics and how much material needs to be removed to achieve the desired surface finish.
Roller and Ball Burnishing
The process of burnishing is the plastic deformation of a surface due to sliding contact with another object. There are many burnishing processes utilized by manufacturers today, however, the most common are roller burnishing and ball burnishing. Burnishing does not remove any material, it is a small-scale forming operation that can improve the finish or hardness of the part’s surface.
Powered Brush, Belt and Disc Deburring and Finishing
These machines come in many shapes and sizes and utilize rotating abrasive discs, brushes and drums to process parts. They are best suited for sheet or plate material since parts are often transported through the processing equipment on a flat belt conveyor. Some of these machines are engineered to produce the directional scratch marks known as a grain on flat sheet metal surfaces. Robots arms can also be outfitted with compliant power tools and bonded abrasive media to process large 3-dimensional parts. These robotic workcells are then programmed to deburr corners and finish surfaces in a repeatable and controllable fashion.
Abrasive Blasting
Solid particles of a selected abrasive media are accelerated, most commonly with compressed air, and directed by a nozzle so that they impact the part’s surface at a high rate of speed. There are many different media materials, sizes and shapes that can be utilized depending on the hardness of the base metal and the surface effect desired. Sand is a common and inexpensive material that is often utilized to clean and texture large metallic surfaces and prepare them for subsequent painting processes. Glass beads, crushed walnut shells, dry ice and baking soda are examples of other media that can be used in abrasive blasting systems. It is common for smaller parts to be placed into an enclosed cabinet for processing. This glovebox enclosure contains the dust generated by the blasting process and protects the operator from the ricocheting media. There are also robotic blasting systems and multi-nozzle machines available that automate the process and improve consistency and material removal rates.
Electrochemical Deburring and Polishing
This is a method that finishes a machined part’s surfaces by means of anodic metal dissolution. A part specific shaped tool is the cathode. In conjunction with an electrolyte fluid, an anodic reaction is created between the tool and the part that removes surface material in a very precise manner.
Thermal Deburring
This process uses the ignition of a combustible gas within a pressurized chamber to remove burrs from machined components. Because the burrs are much smaller than the component, they reach the auto-ignition point instantly and are vaporized in the oxygen-rich chamber. An oxide powder is left across the component surfaces and may need to be cleaned prior to, or as part of subsequent coating processes.
Abrasive Flow Polishing and Deburring
The abrasive flow process uses the reciprocal flow of abrasive laden slurry to polish and deburr the surfaces and edges of a machined part. Two vertically opposed cylinders pump the slurry back and forth through passages formed by the workpiece and special part specific tooling. This process is typically used to deburr and polish parts with complex internal features.
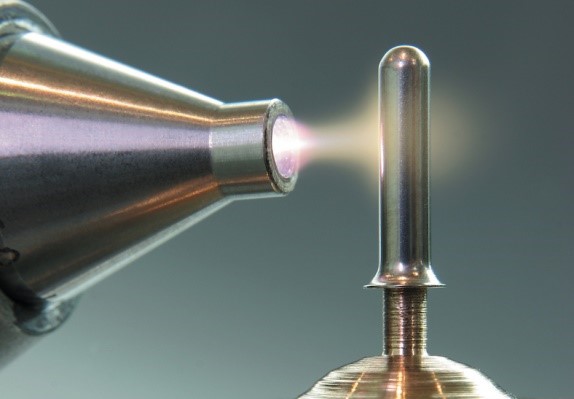
Plasma Surface Treatment
Plasma, the fourth state of matter, is a gas that’s been partially ionized and has been electrically charged with freely moving electrons in both the negative and positive state. Plasma flames can be used for pretreating surfaces of metallic parts prior to subsequent coating, printing or bonding operations. The plasma removes any foreign contaminants present on the surface of a material and also activates the surface at a molecular level significantly improving the adhesion characteristics of the base material.
Keller Technology is a world class manufacturer of vacuum and pressure vessels, process equipment, electro-mechanical sub-assemblies and complex machined parts. Our well-equipped, state of the art manufacturing facility allows us to produce fabrications to exacting dimensional tolerances.
Contact us today with your most challenging fabrication and manufacturing projects.