Automation equipment comes in many different configurations and formats. Lean work cells, hard automation, robotic assembly cells, flexible palletized conveyor systems, semi-automatic manual workstations, or any combination of these types, are common in today’s factories. The possibilities for different machine concepts are truly limitless. The factory automation solution you utilize, to produce a particular product, is most often dependent on the corporation’s high-level goals, however, it is also dependent on the product itself. The design of the product is arguably the single most important aspect of any manufacturer’s production process, regardless of the style of assembly automation chosen.
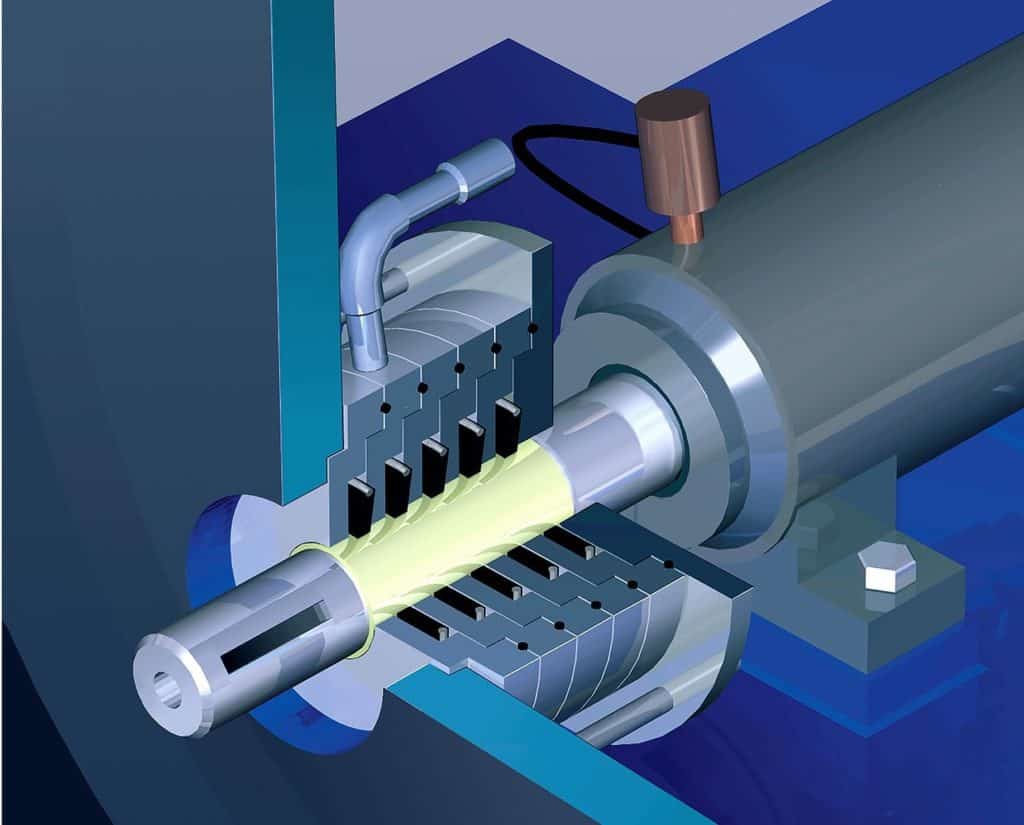
Unfortunately, the product design is often set into stone by marketing and the engineering drawings are frozen before the production group is given the production requirements and cost targets. Many times the assembly methodology that will be used to manufacture the product is not even considered or is an afterthought. It is then up to the manufacturing engineers and machine designers to figure out how to achieve the program goals. This is the wrong approach and at times can be extremely difficult to implement. Many products are designed in a manner such that automatic assembly is unreliable, expensive, or even impossible.
So, what is a better approach? Simple, define the cost targets and production requirements first and communicate them effectively to the entire organization.
- Include production managers and manufacturing engineers on the program team and have them contribute assembly process knowledge and participate in the product design function.
- Utilize tools such as Design For Manufacturability (DFM) to reduce component part and fastener counts.
- Incorporate self-locating features into the parts where possible to reduce the amount of in-process fixturing needed.
- Eliminate all unnecessary redundancy in the design.
- Tolerance parts accordingly and develop the production method and tooling concurrently along with the design of the product.
- Brainstorm and solve potential manufacturing problems before they occur.
By doing this, strong relationships will be formed across the entire organization and everyone will share the high-level process and its successful implementation.
This approach will inherently reduce the cost of the assembly equipment, improve its performance, and shorten the overall program timeline. System integrators and manufacturers of automated equipment and machinery, like Keller Technology, can also participate at the beginning of the product design process and suggest modifications to product features to improve the likelihood of a successful automation project.
Contact Keller Technology to learn more about the latest innovations in machine design and the multitude of ways that these systems can be successfully deployed in today’s modern factory.