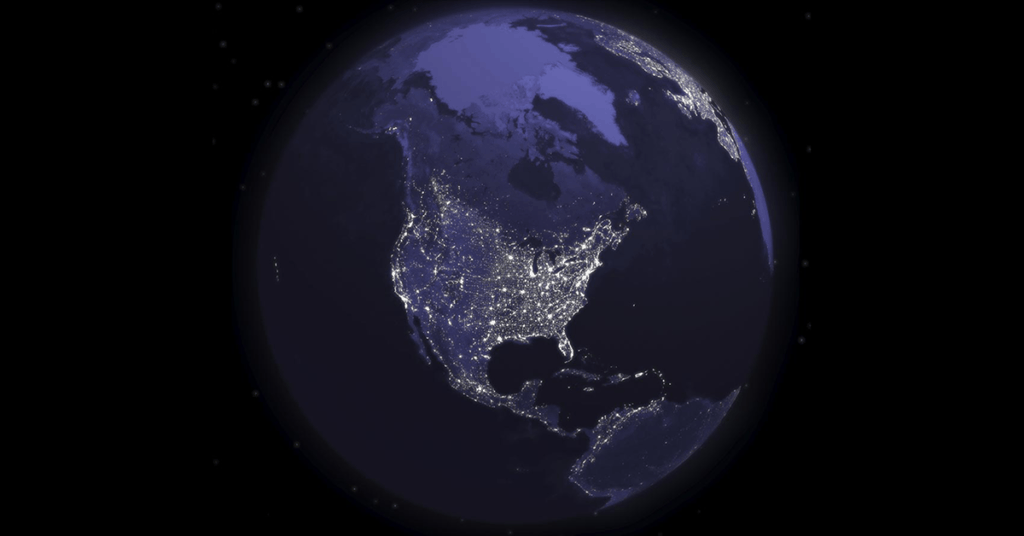
Recent events have exposed the fragility of global supply chains. At the outset of the COVID-19 pandemic, we quickly learned that much of the PPE needed to respond to the crisis was manufactured overseas, especially in Asia. Manufacturers had previously made the decision to produce their products in countries that had lower overall costs stemming from labor, regulation, and taxes. While the PPE situation was very visible at the time, for example, it was not unique. Today we are seeing supply chain issues in many commodity areas for manufactured products.
As we begin to emerge from the grips of the pandemic, global demand has surged while manufacturing capacity struggles to meet it. Logistics costs are on the rise and lead times for overseas shipments are increasing. While it is uncertain when manufacturing and logistics capacity will meet demand, it does appear that these issues will continue for some time.
The situation has forced U.S. manufacturers to consider the true costs of offshoring the production of their products. In some cases, comparative advantage remains with other regions or countries despite the increase in logistics costs and lead times. For many goods, however, current conditions present an opportunity to re-shore production and actually reduce costs in the process. Even if direct costs – the Cost of Goods Sold (COGS) – can’t achieve parity through reshoring, the benefits of doing so may outweigh the COGS differential. Some of these benefits that are not direct COGS, but must be considered, include:
- Reduced lead times. Significant reduction in lead times can reduce or eliminate the inability to fill orders. The opportunity costs of not having product on hand and orders unable to be fulfilled are hard to overstate. Because these opportunity costs do not appear in direct COGS, they are sometimes not identified or considered.
- Agility. As the trend of mass customization grows, the ability to make design or configuration changes on the fly can be a real competitive advantage for those who can successfully execute. The control afforded to manufacturers who bring production in house or to local suppliers can be key to enabling the tactical agility required to win in today’s marketplace.
- Safeguarding of intellectual property. What is the true cost of IP theft or forced appropriation? It is hard to quantify, and the risks are different for each industry or company. Not all regimes respect intellectual property or patents, even to the point of fostering national policies and strategies that involve stealing technology from US companies.
- Lower overhead costs. Reshoring simplifies the supply chain reducing the need for supply chain management, supplier quality engineering, logistics, legal personnel, and expertise. These costs aren’t direct to COGS, but they most certainly hit the bottom line. In many cases, the large overhead burden required to manage large, complex global supply chains when properly applied to direct unit costs may cancel out the direct cost savings realized by manufacturing in low-cost countries.
- Quality. It is much easier and less costly to manage product quality when production is internal or local. The cost of poor quality can be huge and take the form of lost customers, rework, missed deliveries, regulatory compliance problems and more. While many low-cost countries have very high-quality suppliers, the lack of real-time control over quality and difficulties communicating detail and nuance can be very costly.
For many companies, looking at and accurately quantifying the “soft costs” of offshore production requires a shift in mindset. There is always pressure to reduce direct COGS, which is healthy only if it does not create a blindered, myopic view of total cost. A holistic mindset is needed to seek out, identify and attempt to quantify the costs of off shoring. Manufacturers are learning how to leverage technologies such as factory 4.0, robotics, unattended machining, etc. along with lean processes to achieve direct COGS reductions when reshoring. Current events have pushed them to learn how to analyze indirect costs more accurately. This scrutiny has illustrated that in many cases, reshoring yields the lowest total cost.
Looking for a one-stop contract manufacturing partner that can help save on your next project? Request a quote from the team at Keller Technology Corporation to get started.