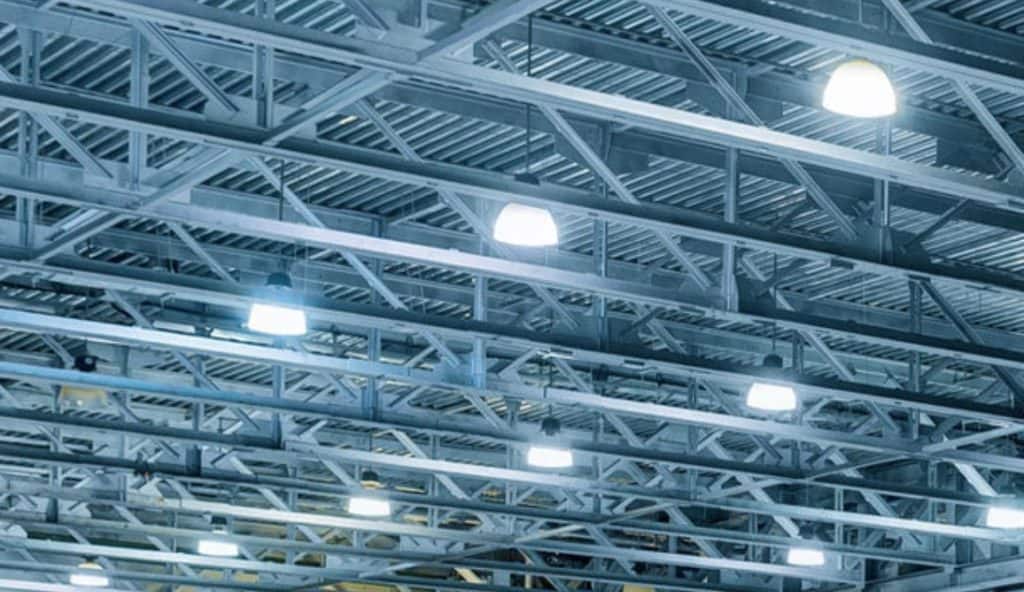
Older manufacturing and metalworking plants can be dark, smelly and dirty places negatively affecting the employees working in this dangerous environment. Air quality standards and guidelines for lighting type, quality, lux levels and placement are available for general industrial environments, as well as a variety of very specific work situations and tasks. Manufacturers have several good reasons to exceed the minimum standards for workplace lighting and air quality, but perhaps the biggest reason is to provide the healthiest workplace possible to attract, retain and protect employees. A clean, bright and orderly facility can also help attract and retain customers that expect their supply chain partners to be “world class” in every way possible.
Industrial Air Cleaner Installation & Benefits
Welding, machining, painting and grinding operations generate dangerous airborne particulates and fumes that can pose serious health threats to workers. Over the past ten years, Keller Technology Corporation (KTC) has strived to continually improve the air quality in our state-of-the-art manufacturing facilities. New machining centers are fully enclosed and include mist collection systems. Industrial air cleaners from Clark Air Systems have been installed in our weld shops and also our grind and polish areas to capture the particulates and fumes created in these work zones. Many assembly areas of the facility are closed off, monitored, and controlled for temperature, humidity, and airborne particulates. Superior workplace air quality also helps make facility cleaning and maintenance easier and less costly, keeping the focus on production.
Facility Lighting & Lux Level Improvements
Improper illumination can also negatively impact both the performance and the quality of work produced by a workforce. Studies have shown that insufficient lighting can have a detrimental effect on the visual perception and accuracy of employees doing detailed tasks. KTC actively monitors lux levels in many areas of our facilities to make sure they meet or exceed internal corporate standards. Lighting and paint colors can have a huge effect on lux levels in an employee’s work area. KTC has seen lux level improvements between 50% and 90% after completing facility lighting upgrades.
Energy use is another consideration and the advanced LED and fluorescent lighting available today offers a better quality of light while using only a fraction of the energy as compared to the light fixtures available only a few years ago.
Keller Technology Corporation’s facilities in Tonawanda, NY and Huntersville, NC provide a safe and healthy workplace for our valued employees and customers. Our continuous improvement program and our many employees strive to achieve “world class” level results in everything we do.