Thank you for visiting the Keller Technology Corporation blog. We take pride in supporting companies with relevant industry information, so sometimes we cover topics outside of our services and capabilities. While we use sensors in the custom machinery and systems we build, KTC is not a sensor supplier.
- Object detection is a critical task in the industrial automation industry.
- Industrial controls engineers and software developers need to know when an object or target has arrived at a particular location.
- The seven most common types of object sensing technologies include electro-mechanical, pneumatic, capacitive and photoelectric.
Whether detecting the presence of an object passing by on a conveyor, the closure of a door, or the arrival of a carrier puck at a stop, object detection is a critical task in the automation industry. Industrial controls engineers and software developers need to reliably know when an object or target has arrived, or been placed, at a particular location. Here at KTC, this type of detection technology is important for our design and manufacturing of automation equipment and custom machinery.
Event-based programming is a very common format and requires these inputs at specific points in the machine’s computer or PLC ladder logic program. While sensing devices don’t measure, inspect or quantify the object in any way, they must reliably communicate the presence or absence of their target to the machine’s control system via electronic signal.
What Types of Automation Sensors Can Be Used for Object Detection Projects?
When selecting an automation sensor to detect the presence of an object, there are many different object sensing technologies. Seven of the most common types of sensors used in automation will be discussed below, along with a brief description of their operation, advantages and constraints.
1. Electro-Mechanical
The most basic sensor is an electromechanical limit switch. These devices contain a sensitive micro switch that changes state when a mechanical actuator is displaced by the detected object. Rollers, whiskers and levers are some of the actuator versions offered by many different manufacturers. Since these devices consist of moving parts, they are prone to wear and damage. Also, physical contact with the target object is not always desirable or possible. This type of automation sensor is used in our precision electromechanical assembly systems.
2. Pneumatic
These sensors utilize compressed air and a sensitive diaphragm valve to detect the presence of objects. Compressed air bleeds from a tiny orifice until the target blocks the stream, creating a minute change in air pressure. This pressure change is detected by a downstream diaphragm switch that produces an electrical control signal. Environments that require an “explosion proof” sensor, or are extremely dirty, are good applications for this type of device. KTC uses this kind of sensor in high-end custom machinery.
3. Magnetic
Magnetic sensors are actuated by the presence of a permanent magnet within their sensing range. Two different operating principles are commonly used, either a reed contact or a Hall effect transducer. In both cases, the presence of a magnetic field produces a change of state in an electrical signal. Reed and Hall effect sensors are often used to detect the presence of an air cylinder’s internal piston. The failure rate of reed switches is relatively high, so many engineers specify Hall effect sensors when possible.
4. Inductive
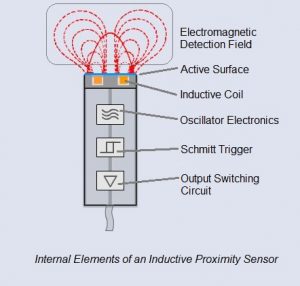
These proximity switches detect metallic objects that cause a disruption in the electromagnetic field emanating from the body of the sensor. The reliable detection distance varies depending on the type of metal and also the amount of metal within the sensor’s range. These automation sensors come in many sizes and shapes. They are very reliable and cost effective; therefore, they make up a large percentage of the sensors used in automation and processing equipment.
5. Capacitive
These proximity switches detect non-metallic objects that have a dielectric constant difference from air. This makes them ideal for a wide range of materials such as wood, paper, fabric, liquid and plastic. Their operation is similar to inductive sensors, but instead of detecting a change in an electromagnetic field, they utilize an electrostatic field. KTC utilizes this kind of sensor in custom automation and processing equipment.
6. Photoelectric
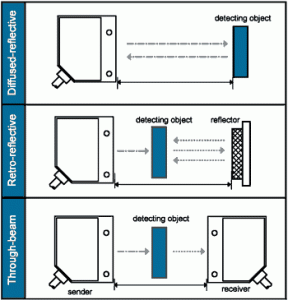
Photoelectric sensors use different technologies that address a variety of diverse application configurations. The common characteristic is that they all send out a beam light and then detect a change in the amount of light received back. The three most popular sensors are diffuse, reflective and through-beam. The light sources used – visible, infrared, LED or laser – will affect the sensing distance. In diffuse sensors, the presence of an object in the optical field of view causes diffused reflection of the beam. The receiver detects the light reflecting back from the object itself. Reflective and through-beam sensors create a beam of light and detect any opaque object that breaks the beam. Laser sensors can create a beam of light 50 meters or longer. Transparent objects, or objects with a varying surface finish, can be problematic for photoelectric sensors.
7. Ultrasonic
These devices typically transmit a short burst of ultrasonic sound toward a target, which reflects the sound back to the sensor. As a type of industrial automation sensor, the ultrasonic sensor is well suited for detecting almost all dense materials (metal, wood, plastic, glass, liquid, etc.) and is not affected by color, transparent or shiny objects. Foam-like materials that absorb sound waves would not be a reliable application of this sensor type. Ultrasonic sensors are often used to determine the level of liquids in processing tanks.
Get the Right Solution for Your Manufacturing Needs
Keller Technology Corporation has decades of experience selecting the best sensing technology and device for use in industrial automation and process equipment. Contact Keller Technology to learn more about possible solutions to your most challenging custom machinery and manufacturing problems.
As a reminder, please note that we are not a sensor supplier.