When designing a machine or LEAN work cell to assemble a product, it is very common for the engineering team to break a complex assembly process down into the individual elements required to complete the job. These elements or tasks may be manual, automated or a combination of both. They can also be quite different from each other and require unique tooling, feeding systems, processing equipment, orientation mechanisms and holding fixtures. Automated parts handling systems are essential for parts to flow smoothly.
For example, consider this hypothetical assembly and test sequence. A component needs to be automatically picked from a tray, dipped into an adhesive, inserted into a hole in the part, accurately oriented, heated to cure the adhesive, cooled down to room temperature, flipped over, leak tested and labeled. The part is then secure and safe for an operator to visually inspect it and place it into outgoing dunnage for transfer to another part of the plant. It would be impossible or highly inefficient to do all these tasks in a single workstation, so the engineers decide that multiple automated material handling workstations will be utilized to perform this work in the allotted amount of time.
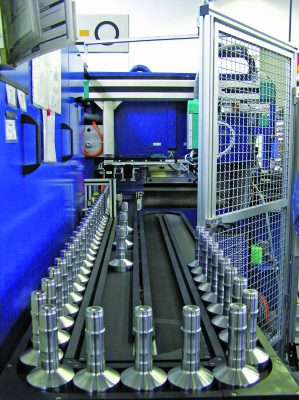
12 Part Handling Automation Solutions
Check out 12 of the most common methods of factory part transfer methods in automation and their advantages, disadvantages and constraints:
- Manual Transfer – The most basic and common material handling transfer method is for a person to hand or slide a single part across the table to the person working next to them or to load it directly into the nest of a machine. In a LEAN work cell, there may be a designated spot or fixture for the placement of a single workpiece. This system of transfer is known as “one-piece flow” and it keeps WIP, or “work in process,” to an absolute minimum. When it is not safe for a person to manually move parts or when there isn’t time available, other automated means must be utilized.
- Gravity Roller Conveyor and Slides – These are often used to provide a limited queue of parts between manual workstations or to supply an automated machine with the components needed for the assembly process. The conveyor or slide is angled so that gravity provides the force necessary to move the parts within the confines of the conveyor’s side rails. It is a very common method used in manual work cells when the part has a flat surface and an accommodating center of gravity.
A variant of this method is vibratory rails and tracks. Instead of gravity, vibratory motion is used to move the parts forward. Part orientation can sometimes be maintained utilizing the geometry or unique clocking features of the part. One disadvantage of this method is the potential for part damage due to part-to-part contact, sliding and collisions. - Walking Beams – Beams can be powered by pneumatic cylinders, hydraulic cylinders, servo-driven actuators or cam motion. The indexing linear motion is synchronous and all the parts in process are advanced to the adjacent downstream workstation holding nest simultaneously. The parts can be lifted from below by rails or from above with an array of grippers. Another variation of this concept is to slide all the parts utilizing forked tooling that advances and retracts from behind the part. Walking beams can be a very efficient solution to moving a lot of parts with a minimal number of actuators in a small, in-line, footprint.
- Rotary Part Handler – A “cambot” utilizes a smooth, cam actuated, indexing or oscillating motion. Similar to a walking beam, all of the parts are moved from nest to nest simultaneously by an array of grippers, however, the motion is rotary instead of linear. The main advantage of this transfer method over a rotary dial is that the holding fixture at each station can be unique. At times, that is a big advantage for the machine designer.
- Robotic, Servo or Pneumatic Pick & Place Transfer – There are limitless variations of this method of transferring parts. Generally, one part is moved at a time and the motion is non-indexing and asynchronous. It is similar to the manual transfer of parts but the automated version. Pick and place mechanisms can only move parts from point A to point B.
The advantage of using a robotic arm or Cartesian robot is that it can be programmed to move parts to multiple points. A robot is commonly used to move parts from an incoming tray, into the process holding fixture for work to occur, and then into a completed part tray or output conveyor. Robot programs can also be easily changed to accommodate future modifications to the workstation. - Precision Link Indexing Chassis – This indexing, synchronous, part transfer method utilizes many part-holding nests that are attached to the links of a high precision, guided, loop of roller chain. When the chassis is signaled by the controller to index, the chain and all the nests attached to it move the parts a precise distance to the next station. After the work is complete, the chassis indexes again. Precision link chassis is available in two configurations, side by side and over-under.
It is also very common to utilize a single cam motion for both the chassis index and to power many of the workstation actuators. These systems are advantageous for high throughput assembly automation that will make a lot of the same part. They are not as easy to reconfigure or change so generally they are used when the assembly will not need frequent modification or design changes. - Indexing and Reciprocating Rotary Dials – Rotary dials are a relatively inexpensive way to transfer parts quickly and accurately from station to station. In the past, many dial plates were powered by cam actuated indexers with a set number of stops. More recently, servo motors and gear boxes are being utilized. This allows a controls engineer to program the number of stops allowing for future flexibility to add stations or reverse direction. Machine designers utilize this transfer method to assemble many different products.
A disadvantage of this method is that all the nests must be identical. For high force press operations, the dial plate needs to be supported or the part must be lifted out of the nest and supported from below. Dial plates can only be so large, so if the workstations are wide, you may need to add extra blank stations between process stations. Future flexibility, to accommodate product changes, is also somewhat limited with this transfer method. Also, maintenance accessibility can be challenging due to the compact nature of these machines. - Powered Roller & Belt Conveyors – These transfer devices are utilized more often for material handling tasks as opposed to assembly automation but there are exceptions to every rule. Belt conveyors can move parts into an assembly station where they are located with a vision system and picked up with a robot. Conveyors can also have alignment tooling attached directly to the belt which facilitates accurate location of the parts. Powered roller conveyor or mat top roller conveyor can also move parts from station to station in an assembly system although it is more commonly used in a warehouse setting to move pallets or boxes of product that is already assembled and packaged.
- Power & Free Overhead Chain – Overhead chain systems utilize trolleys captured in a track hanging from the ceiling. The trolleys are powered via a continuous loop of moving chain integral to the track. These systems often have larger parts hanging from a hook. One common use is for moving parts through automated paint lines or for moving assembled parts long distances from the manufacturing line to a packaging area.
- Recirculating Pallet and Puck Conveyors – These are often used to transfer parts and assemblies within an integrated assembly system. It is typical to utilize precision tooling to locate the assembly in a known location on pallets. Pucks are often used instead of pallets if the system is handling cylindrical parts. In both cases, pucks and pallets circulate throughout the powered conveyor system from station to station.
Friction and continuously moving belts or side flexing chains are used to transfer power for moving the pucks and pallets through the system. These systems are asynchronous, so the pallets or pucks can accumulate in queues prior to entering each station. Pneumatically-controlled stops and pre-stops are used to control the flow of pallets and pucks through the system. When precision location is needed at a particular station, a “lift and locate” mechanism is used. There are an endless number of conveyor configurations possible and this is a huge advantage of this type of part transfer system. - Motorized Pallets and Linear Motor Transfer Systems – A motorized pallet system differs from a recirculating pallet system in that the pallets themselves are individually powered. Each pallet carries a small motor that is powered via an electrified rail in the conveyor. Linear motor transfer systems are becoming more mainstream than they were just ten years ago. Each pallet contains a powerful magnet and a linear motor embedded in the conveyor modules can move pallets extremely quickly in both directions.
- Guided Vehicles – These are typically used for material handling as opposed to automation but, with vision and robotics becoming more common, that is changing rapidly in modern factories. Available in many shapes and sizes, automatic guided vehicles, or AGVs, can move trays, bins, boxes or an entire section of an airplane around a factory. These vehicles are controlled by computer and use a series of sensors or on-board cameras to determine their location and speed. They also use cutting edge technology to determine when obstacles or people are blocking their path.
Let Keller Help Solve Your Toughest Automation Challenges
Keller Technology Corporation has decades of experience selecting the best parts handling devices to use in custom engineered industrial automation. Contact Keller Technology to learn more about possible solutions to your most challenging manufacturing problems.