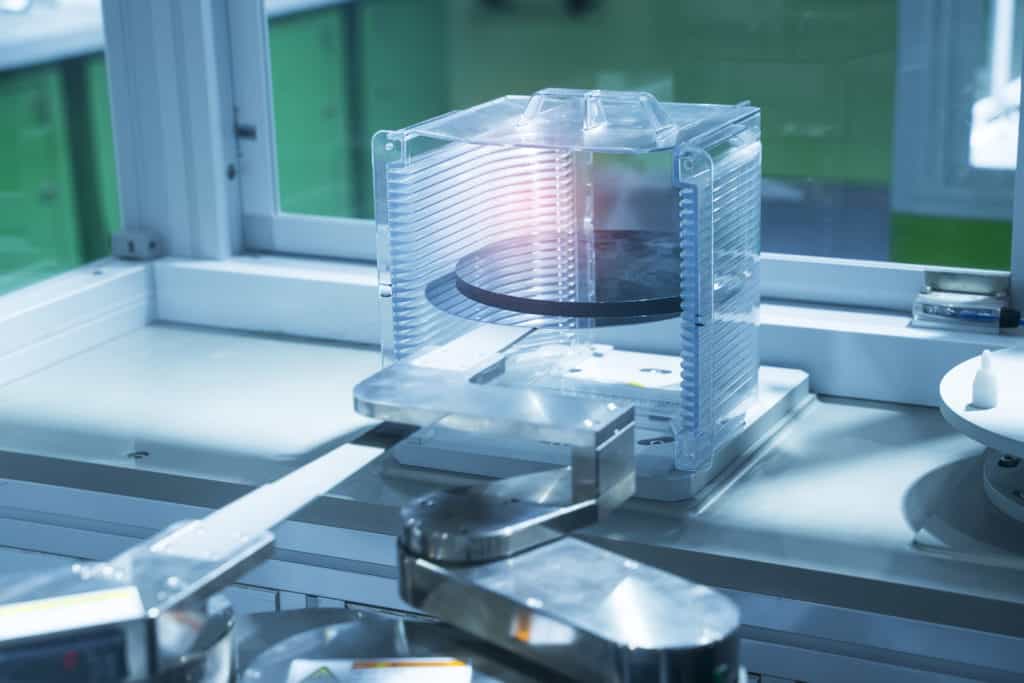
Virtually, all semiconductor equipment OEMs outsource at least some of the content of their product to machine shops, fabrication shops and/or sheet metal shops. The benefits of outsourcing are clear: tool producers can leverage comparative advantage and specialization in the supply chain.
Increasingly, tool manufacturers of various sizes are beginning to see the advantages of sourcing more high-level content to specialized contract manufacturers. These highly integrated electromechanical assemblies are commonly referred to as modules or high-level assemblies (HLAs).
Minimizing Volatility & Downturns
The semiconductor industry has previously been known for its cyclical demand and sometimes violent ramps and downturns. For a tool supplier, a smaller internal manufacturing footprint enabled by outsourcing high-level content can help in navigating through this volatility. Tool companies can maintain a smaller staff with less real estate in the form of manufacturing facilities. Lower fixed costs help weather the downturns and the flexibility afforded by the outsourcing of HLAs allows for a quick ramp with minimal capital investment or hiring.
Simplicity & Efficiency
Outsourcing of HLAs, as opposed to outsourcing many disparate parts, also serves to consolidate and simplify the supply chain. There are real efficiencies to be had because fewer parts to buy means fewer PO’s to cut, track, expedite, along with considerably less logistics management; reducing the overhead required for the manufacturing planning and supply chain management functions.
With a simplified supply chain and fewer incoming parts, the assembly floor becomes simpler, more organized and easier to manage. Larger modules coming in allow for a more efficient use of space and fewer inventory SKUs to keep up with.
External Functional Testing
Pushing more of the content out to suppliers can also allow for the functional testing of modules to be done externally. Typically, modules will not be shipped and delivered until they have passed the specified test protocols. Errors and problems tend to be caught and remedied at the supplier as opposed to creating production flow problems on the semi tool OEM’s floor.
Transitioning towards sourcing higher level modules and HLAs does require some effort and coordination. The organization needs to be aligned and working toward the same goal. Supply chain management must work closely with manufacturing and engineering as the OEM moves toward bringing in more vertically integrated content. All stakeholders need to be able to share their needs and constraints with each other. There may need to be some changes made within the company’s ERP/MRP system as well as with the structure of its manufacturing drawings. If an OEM had formerly been doing most of the assembly, there is tribal knowledge that may need to be captured in the form of work instructions. The drawing package needs to be updated and maintained to accurately reflect the desired as-built condition of the equipment. There also may need to be some investment in training the supplier on the assembly and functional testing of the modules. A co-build at the OEM’s site with the supplier’s technicians is an excellent way to efficiently transfer legacy knowledge.
Contract Manufacturing Solutions
Being in an industry that’s always changing, Keller Technology Corporation is backed by 100 years of engineering and equipment manufacturing expertise. From turnkey equipment to controlled-environment clean room assembly, our team can help with any aspect of your contract manufacturing project.