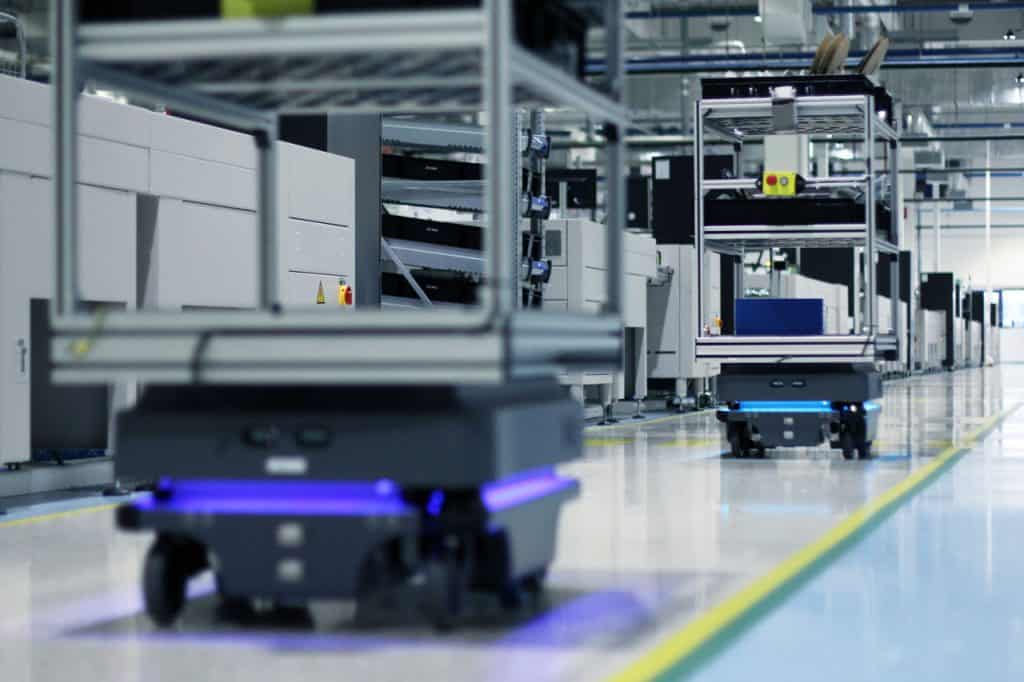
The global economy, corporate onshoring initiatives and recent shifts in supply chain economics has caused a huge surge in demand for assembly automation and robotic work cells. Material handling, the movement of raw materials and product around the factory, is also becoming increasingly automated. The surge in warehouse automation is expected to continue for a number of years due to a number of factors, including the boom in e-commerce, advances in technology, a decrease in the cost of computing power, and the increasing cost or unavailability of labor in many areas of the world.
Automatic Guided Vehicles (AGVs)
One means to automate material handling in a factory is by using unmanned robotic vehicles to move products from one location to another. Automatic Guided Vehicles, or AGVs, are powered, mobile, robots that are programmed to move goods around a facility. They rely on devices such as floor markers, buried wires, magnets, lasers, or cameras to guide them on their pre-programmed path. They stop and pause at designated locations and can continue their journey after a set amount of time has elapsed or via a pushbutton input. The AGV’s on-board sensors detect obstructions in its path and trigger the vehicle to stop automatically to avoid collisions with obstacles or humans.
AGVs have been around for more than 40 years and their job is to simply move materials along the same path within the facility. One very common AGV, developed years ago, delivered mail in office buildings. When you heard the familiar beeping, off in the distance, you knew the mail was on its way.
Autonomous Mobile Robots (AMRs)
Within the last five or six years, Autonomous Mobile Robots, or AMRs, have evolved quickly and are becoming more and more common in warehouses and distribution centers. AMRs are similar to AGVs but with one main difference. In the factory of the future, AMR users program destinations into the system, not a specific path. Each vehicle determines the path it will take, from point A to B, on its own using significant computing power, artificial intelligence and an array of sophisticated cameras, lasers, and sensors. Machine learning capabilities enable the robot to become more efficient and accurate over time as it encounters new situations during day to day operations. Regardless of the technology in use, the goal is the same – a vehicle that can direct itself around an environment without hard guidelines.
There are many different AMR configurations designed by engineers to handle a wide array of goods and materials. Many AMRs are low to the ground and are designed to lift or “tug” an entire shelf or cart of product. Other AMRs are configured like hand lift trucks and move a standard pallet via a pair of forks. Some AMRs have attached shelves or racks, and some are even large enough to move entire sections of a passenger jet fuselage.
Successful implementation of an automated material handling system, guided vehicle, or mobile robot requires an accurate assessment of your needs and the technologies best suited for the task. Contact Keller Technology to learn more about material handling automation and the new ways it can be used in today’s modern factory.