High speed machining (HSM) has come a very long way since its conception in the early 20th century. Early adoption of the concept was slow, but in the early 1980s, the HSM process got a jump start as aerospace companies started making investments in research and development to further advance the technology. In the last 20 years, huge strides have been made in a relatively short period of time and HSM has now achieved widespread acceptance by today’s manufacturers. The future of high speed machining was envisioned by the process inventors when they discovered that after a certain point, increasing the cutting speed actually reduced the heat in the cut. The graph below (Fig. 1) from Dr. Herbert Schulz’s “History of High Speed Machining” illustrates this phenomenon perfectly.
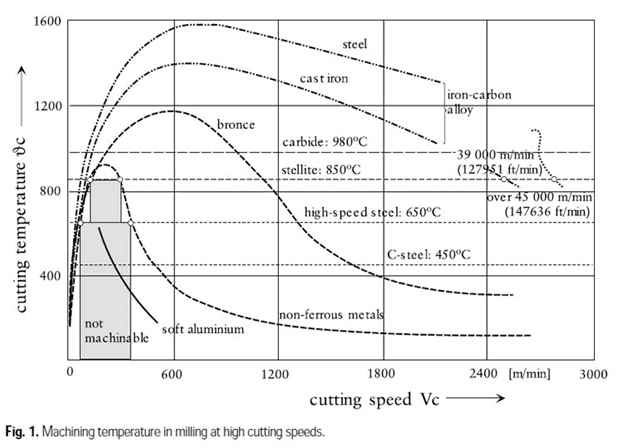
The dotted lines represent temperatures of various metals at different surface speeds. Temperatures rise steadily with increasing speed until they peak and start going down with higher rates. One of the big advantages of high speed machining is that at elevated rates of speed and feed, the chip is cut and evacuated so fast that it transfers little or no heat to the green workpiece.
The best way to describe modern high speed machining is the definition coined by Modern Machine Shop Magazine. They stated that HSM “refers to making light milling passes at high spindle speed and feed rates to achieve a high metal removal rate.”
In practice, high speed machining is a collaboration of equipment, tooling, software, and techniques that machinists and CNC programmers use to continually improve machining efficiency in today’s modern machine shops. Advanced computer programs running on relatively inexpensive and powerful computers have made many of these rapid advancements in efficiency possible. What may have been considered HSM only a few years ago, could now be considered standard speed machining.
Some of the more common HSM practices, techniques, and tooling found in use today are:
- Using a single pass by combining the roughing and finishing passes used in traditional machining.
- Utilizing smaller diameter tooling at higher rotational speeds, moving at faster feed rates than the traditional large diameter, slower rotating tools.
- Programing lower cut widths typically less than 15% of the cutting tool diameter.
- Using High Efficiency Milling (HEM) strategies such as trochoidal milling
- Selecting optimum spindle speeds that maximize stable milling zones.
- Utilizing advanced machines, spindles, cutting tool materials, setting & balancing equipment and rigid work holding systems.
As a trusted supplier of precision CNC machined parts and complex process equipment for many of the world’s largest OEMs, Keller Technology Corporation is continually improving our internal processes, tooling and CNC machining equipment. Contact KTC today to discuss how we can handle your most challenging manufacturing projects.