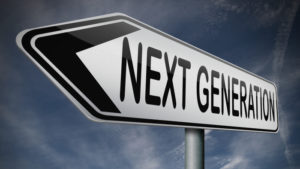
- Keller Technology co-developed a next-generation laboratory diagnostic instrument.
- Having built the first-generation instrument allowed Keller Technology to integrate improvements into the new design.
- Value analysis allowed for cost containment and reduction while engineering the new instrument.
While unable to share specific project details to protect our customer’s intellectual property, we would like to share some important insights found while co-developing a “next generation” laboratory diagnostic instrument along with our customer.
In developing the version 2.0 instrument, Keller Technology Corporation had the opportunity to develop the next iteration of an instrument, where the consumable utilized on the machine was to remain constant. No change to the consumable cartridge allowed for a faster equipment development cycle, but also limited the possibilities for improving the instrument in certain areas. Having the opportunity to build the first generation provides the advantage of integrating lessons learned from the original device into the new design. Some of the major steps taken to realize the design of the new instrument included:
- Voice of Customer (VOC) – Our customer was able to provide us feedback from end users of the legacy instrument to inform our design. Some of the VOC feedback included human factors ideas, as well as direction on how to improve the HMI for a better user experience.
- Design for Manufacture (DFM) – Opportunities to improve the manufacturability of the legacy design were used to optimize the design of the next-generation instrument. The new instrument’s preliminary design was then subjected to DFM activities, including part-count reduction where possible.
- Cost Containment and Reduction – The original instrument was analyzed to determine which features and components provided value and were worth the cost they represented, and which were not. Our customer’s input was critical to this step of the process. They alone had access to the end user customer and the specific knowledge used to determine the functional requirements and critical features of their product, and it was incumbent upon them to determine the parameters and boundaries for the value engineering process. Upon completion of the value analysis, those conclusions were used in the value engineering of the new instrument, allowing us to realize a design that represented the optimal value achievable within the price targets as given by the customer.
Once a stable design had emerged, we were able to move forward and manufacture the prototype unit. The prototype was able to be tested to identify areas for improvement. While refinements to the prototype were made, reiteration was minimal due to the careful attention paid to the early-stage development steps.
Since the instrument was for a non-clinical application, this development program did require our ISO 13485 SOPs which we utilize for programs subject to cGMP. Considerable skill was required to design and build this large, complex instrument, which required expertise with design and integration of systems comprised of fluidics, precision motion control, optics, and opto-mechanics.
The instrument was manufactured in pilot-scale quantities at first and then moved into full-scale production with final assembly, integration, and assembly being done at Keller Technology. We were able to leverage our global supply chain operation to optimize value to our customer.
Keller Technology’s niche is the manufacturing or development and manufacturing of complex electro-mechanical instruments and equipment. Contact us if you are seeking an experienced manufacturing partner or require the development of your next-generation instrument.