Thank you for visiting the Keller Technology Corporation blog. We take pride in supporting companies with relevant industry information, so sometimes we cover topics outside of our services and capabilities. While we use marking methods in the machines and systems we build, Keller Technology Corporation does not provide marking methods as a standalone service.
- Part marking systems are often integrated into lean assembly cells and custom automation equipment to enable accurate part identification.
- Application of choice depends on the product material, functional requirements, budget, production rate, and end-use environment.
- Nine common marking processes include paint dot and hot stamp.
Part marking systems are often integrated into lean assembly cells and custom automation equipment to enable accurate part identification. While there are multiple technologies and options available for engineers to consider, the method you select for your marking application depends on the product material, functional requirements, budget, production rate and end-use environment.
Let’s explore nine common industrial part marking processes used for part identification and some of the considerations for each method:
1. Pneumatic Impact – As the name implies, this type of marking system utilizes a striking blow, along with a hardened steel punch, to produce a permanent mark on a designated area of a malleable part. Powered by compressed air, the marker uses an impact force to displace a small amount of the base material forming a depression. This method can be noisy and isn’t suitable for fragile parts that could be damaged by the tool’s impact.
2. Paint Dot – This part marking system transfers a small, generally round spot of contrasting paint or ink onto a part. Whether dabbed or sprayed, the dot is a human-visible verification that a process or inspection has occurred. Spray nozzles, air cylinder-mounted markers, or actuated rubber stamps are common mechanisms utilized for the transfer of the paint or ink to the product. Although suitable for fragile parts, there are some disadvantages to using paint or ink to mark parts.
The paint or marker needs to be purchased and stocked. In addition, since it is a wet process, there are strict maintenance and housekeeping rules necessary to keep the paint from drying out, clogging up nozzles, or making a mess. Drying time, adequate contrast, ventilation and longtime durability of the mark also need to be considered before selecting any paint or ink marking system.
3. Rubber Stamp and Pad Printing – Relying on paint or ink, this part identification solutions involves using a round rubber bladder or stamp to transfer the wet ink from the printing machine’s plate, or cliché, to the part.
Pad printing is often used on larger injection-molded plastic parts when the product has curved surfaces and fine detail is required. While it is a relatively fast process, this industrial marketing solution does require custom stamps/tooling, rubber type, and a manual set-up for each part variant being processed.
4. Roll Press and Steel Stamp – Both processes utilize steel stamps and brute force to displace the base material and leave a permanent, human-readable mark on a part. A rolling action can be used for multi-character marks if the single stroke marking force is too high. Most often this system is used for larger, metal parts or bar stock that require a long-lasting mark and a short marking cycle time. Since changing the stamps in the holder is a manual process, this industrial marking solution is often used for batch runs and is not suitable for parts requiring serialization. While relatively fast and inexpensive, this system is limited to parts that can withstand the higher pressing force of the marking process without damage.
5. Hot Stamp – Similar to steel stamp marking, this thermal based part identification system involves tooling that is heated to a temperature above the melting point of the base material. Typically used on injection-molded thermoplastic parts, the material melts where the characters come in contact with the surface. This process minimizes the force required to displace material; however, the melting material usually creates smoke as it burns, requiring additional equipment to contain and remove the potentially toxic fumes.
6. Rotary Engraving and Scribing– Both of these systems utilize multi-axis motion to “carve” a mark on the product. A single point tool, rotating in the case of the rotary engraving machine, removes or displaces the base material creating a permanent mark on the part. This method is somewhat slow and automation of the process requires a relatively expensive programmable machine. Serialization of parts and incorporation of artwork or logos is also possible.
7. Dot Peen – Related to engraving and scribing machines, dot peen marking systems are programmable machines that strike the product’s surface with a carbide stylus that displaces a small amount of material with each hit. Multiple hits form a dot matrix resulting in a low-resolution, permanent mark. 2D barcodes, serial numbers, lot identification or logos are common applications. This method is relatively slow and can be noisy if the part is allowed to resonate. In addition, the mark quality can vary depending on the hardness of the material, support tooling, and stylus wear.
8. Ink Jet – This high speed part marking method is very common in high-speed packaging lines, ink jet printers require relative motion between the part and the print head to function. As the part and print head pass each other, at a constant rate of speed and distance, droplets of ink are fired from the head’s nozzles, forming a matrix of small dots on the part’s surface. These systems are programmable, fast, and suitable for part/lot serialization, but they are also relatively expensive. Like all of the methods that utilize paint or ink, the wetted components require diligent maintenance.
9. Laser – The costs associated with laser part marking systems have come down considerably in recent years. Using a fiber laser to mark industrial parts does have some distinct advantages over other systems. It is appropriate for metals and plastics, has high resolution, is programmable, and does not require a consumable ink or paint. The disadvantages are system cost, laser safety considerations, fume extraction, and issues marking highly reflective surfaces.
Find the best automated choice for your equipment
When it comes to automated system solutions, like industrial part marking methods, Keller has the design and build and build-to-print capabilities to engineer and bring to life the exact equipment you need. Visit us near Charlotte, North Carolina, or Buffalo, New York, to see us in action.
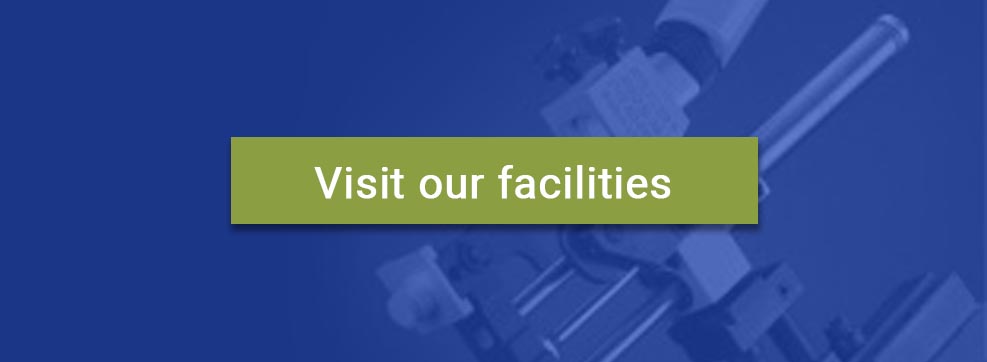