- Medical device manufacturers can benefit from outsourcing high level assemblies.
- Contract manufacturers (CMs) should hold ISO 9001 and ISO 13485 registrations.
- The chosen CM should have a well-developed supply chain.
For some producers in the medical industry, particularly those manufacturers of large, capital medical equipment, it may be impractical or impossible to outsource the entire system turnkey. However, a medical device manufacturer may still be able to benefit from outsourcing by selecting high-level assemblies (HLAs) to outsource.
There is no need to be apprehensive: Precision medical assemblies are subject to the same rigorous quality standards as more fully-integrated equipment and instruments. Outsourcing at the highest level practical is advantageous, and may result in the simplification and optimization of both the medical equipment manufacturer’s factory floor and supply chain.
Here are five things to keep in mind when pursuing this approach:
- Utilize a qualified contract manufacturer (CM). The CM should have a robust Quality Management System. Typically medical device companies will look for CMs that have facilities holding ISO 9001 and ISO 13485 registrations. Additionally, look for contract manufacturers that are well established, experienced, and have a track record of successful programs.
- Invest the time to provide and communicate clear, accurate documentation to the CM. It is critical that the manufacturing drawings, bills of materials, work instructions, and test protocols are detailed and accurate. A joint review of the documentation by both parties before moving forward is critical; missing information, redlines, non-documented knowledge and critical processes need to be captured. In many cases, a co-build of the assembly either at the manufacturer, contract manufacturer, or both is advisable. There is no substitute for hands-on experience to further flush-out important characteristics of the assembly build and supporting documentation.
- Choose a CM with a well-developed supply chain and supply chain management system. High-level assemblies for medical equipment are typically integrated from a diverse variety of components – PCBAs, sheet metal, wire harnesses, machined parts, commercial components, etc. While having internal capabilities is important, no CM can make everything. The ability to quickly, easily, and economically obtain required BOM components is key. An existing supply chain, filled with previously vetted, approved, and monitored suppliers will be critical to the success of a contract manufacturing program. This is particularly important when demand fluctuates or ramps. The supply chain management system must be robust from the outset. Playing catch-up is difficult.
- Establish responsibility for documentation control. In many cases it makes sense for the contract manufacturer to “control” the drawing package to update red lines, manage component obsolescence issues, etc. Sometimes for regulatory or IP reasons, the medical device OEM chooses to retain control over documentation. In either case, the most important thing is to define the scope of responsibility and ensure that related procedures are clearly defined.
- Outsource assemblies at the highest level of integration possible. To maximize the benefit that comes with outsourcing, such as supply chain reduction and simplifying your factory floor, outsource to the highest level module or assembly that is practical. Place one purchase order, and receive a fully-tested module ready to be integrated into the final assembly of your equipment.
Find out more about our work in the medical industry
From pharmaceuticals to surgical equipment, KTC provides solutions for a variety of medical industry sectors. Contact our team to find out how we can manufacture what’s next.
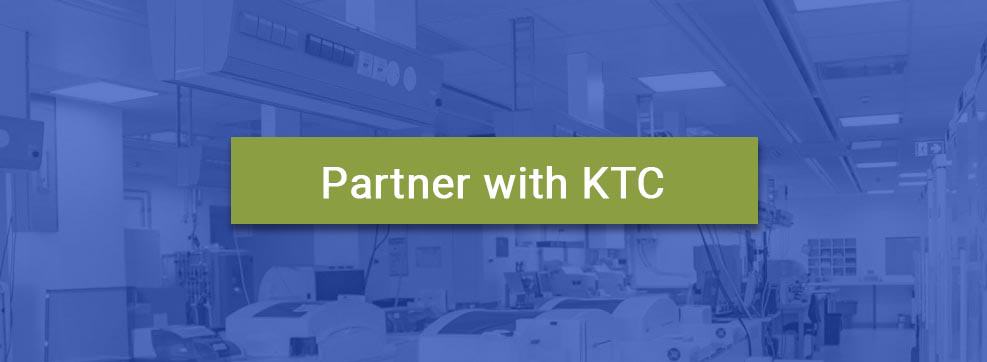