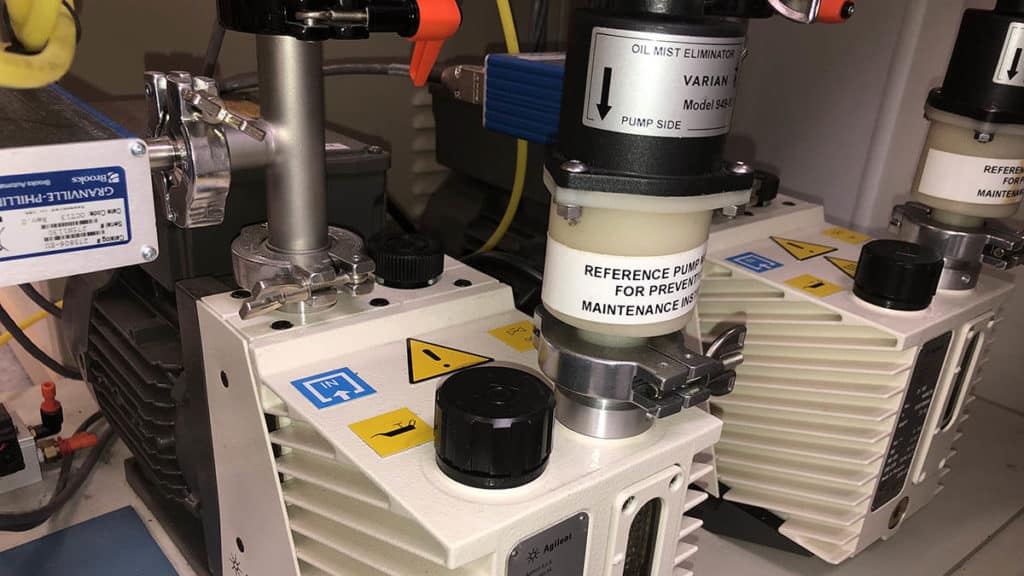
When designing your vacuum system, one of the most important choices you need to make is the type of pump(s) you’ll use.
When designing your vacuum system, you want a pump that will remove gas particles, not introduce contaminants, and not affect its surroundings by introducing stray electric or magnetic fields.
Ideally, pumps should be compact, easy and inexpensive to use and maintain, environmentally friendly and reliable. Some pumps can be used starting with the system at atmosphere, and some require a greatly reduced system pressure before they can operate. Depending on the pressure specification of your vacuum system, you may need to combine multiple pumps to achieve your desired vacuum level.
Pumps can be categorized in many ways, from the vacuum range they work best in, to the way they remove gases from the system.
Pumps can be characterized into two main classes: transfer and capture. Transfer can be further divided into displacement pumps (gas is mechanically separated and compressed with each pump stroke) and momentum transfer pumps (gas particles are driven out through the pump exhaust by high-speed vapor jets or rotor systems).
Examples of displacement pumps include rotary vane, liquid ring, claw and roots, while examples of momentum transfer are diffusion and turbomolecular pumps.
Capture systems trap gas particles and often have finite pumping capacity.
Examples of capture systems include sorption pumps, cryopumps, getter pumps and sputter-ion pumps.
Pumps are also categorized by their effective vacuum range. Rough pumps can be used from atmosphere and generally attain a system pressure of ~0.1 Pa. Examples include diaphragm pump, liquid ring pump, rotary piston or rotary vane pump, steam jet pump and sorption pump. Lower pressures can be attained by diffusion pump, turbomolecular pump, cryopump, and sputter-ion pump, however these cannot be used from atmosphere. For ultimate pressures below 0.1 Pa, a combination of pumps must be used.
The final classification we’ll discuss is wet vs dry. A wet pump is sealed by the presence of a liquid pump medium, and a dry pump is not. There’s always a risk of oil backflowing into the system and presenting contamination with wet pumps. However, depending on the application and sensitivity of your system this may not be a problem.
When selecting a pump, pay careful attention to the specifications provided by the manufacturer.
Manufacturers provide many specifications regarding the operating parameters of their pumps. While searching for the ideal pumps for your system, you may come across any/all of the following:
- Throughput: the amount of gas which passes the inlet port of a pump per unit time (Pa*m3/s)
- Pumping speed: volume of gas discharged per unit time (m3/s, l/s, or m3/hr)
- Ultimate pressure: pressure at which equilibrium exists between pumped gas and back-flow, or the pressure at which the net pumping speed is zero (Pa)
- Compression ratio: ratio of exhaust pressure and ultimate pressure (K0)
- Gas type dependency: certain gases and vapors can be pumped better or worse by different types of pumps
- Working range: pressure range where the pump manifests its optimum pumping speed
Custom-made integrated vacuum assemblies
With a well-versed manufacturing staff and decades of experience, KTC has the skills and ability to provide you the best solutions for your vacuum chamber and system requirements . Interested in seeing how we can help you?
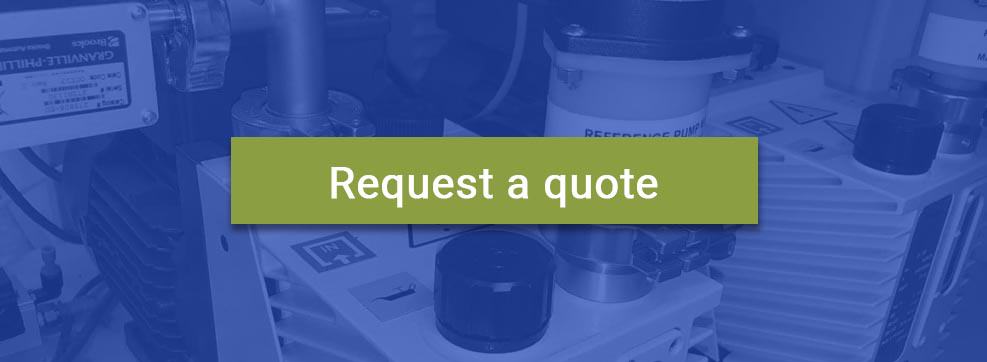