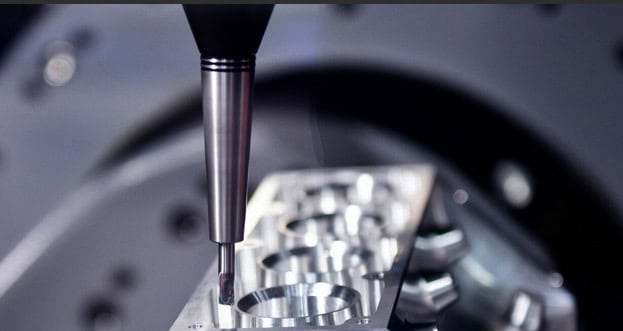
Maintaining a high level of quality throughout the entire manufacturing process is a critical component of successful and efficient production. It begins with the procurement of raw materials, ensuring they meet rigorous standards and specifications to lay the groundwork for a quality end product. As the materials move through each stage of the manufacturing workflow – from initial processing and assembly to packaging and distribution – comprehensive quality control measures must be implemented at every checkpoint.
Equally important is the cultivation of a quality-focused mindset among all employees, from the executive leadership to the shop floor workers. When everyone is empowered and incentivized to uphold quality as the top priority, it becomes woven into the very fabric of the organization’s operations. With unwavering commitment to quality at each step, advanced manufacturers can minimize waste, maximize productivity, and deliver consistently reliable products that meet or exceed customer expectations.
Keep reading to find out how to create a culture of consistent quality, where team members genuinely care about the quality of their work and make decisions based on achieving that level of quality.
Use a Team Mindset
Enhancing quality cannot be achieved solely by individuals. For genuine and significant transformation in advanced manufacturing processes, a collaborative effort is necessary. By including diverse fields in the quest for better quality, a range of viewpoints is gained. Additionally, understanding the history of the advanced manufacturing process is crucial. What led to the current state of the process? There’s likely a reason behind it, and that reason should be examined to avoid repeating past issues. By considering history and collective insights, substantial enhancements can be achieved.
Develop Organizational Understanding of Quality
The key is to understand what quality means to your company, or even better, what it means to your customers. Leaders must have conversations about the concept of quality and establish a definition. Foster an environment where employees embody quality in everything they do—where they are deeply committed to quality as a personal principle, creating a “genuine culture of quality.” This is a setting where employees not just adhere to quality standards but also observe their peer’s prioritizing quality, listen to discussions about quality, and experience quality in their surroundings.
Key Concepts to Ensure Understanding
- Make others feel they are on your team
- Say less, mean more
- Avoid jargon
Be a Quality Leader
Be the quality you want to see in your employees and in your company. Rather than enforcing standards of excellence, transform it into a lifestyle. Be sincere in your conviction about the positive impact your team is making for the company’s benefit, and this will foster trust and commitment from your team towards the company’s understanding of consistent quality and its objectives for quality. Your role as a leader, not merely a manager, will motivate them to act ethically and effectively. It’s akin to the well-known saying: actions speak louder than words.
Drive Quality in All Your Processes
The first step in integrating quality into your processes and products is to define what quality means for your project, your customer, and your stakeholders. It’s crucial to identify the specific requirements, standards, expectations, and methods that will guide your planning, assurance, and management of quality. Tools such as quality checklists, quality function deployment, and quality audits can assist in identifying and documenting your requirements for consistent quality. You must also handle quality adjustments, which are any necessary changes or modifications to your processes and outputs due to changes in your quality standards, expectations, or performance. It’s vital to implement a systematic and structured approach to managing quality adjustments, which involves identifying, evaluating, approving, implementing, and verifying them. Use tools like change requests, change logs, change control boards, and change management plans to manage and document your quality adjustments.
Never Stop Learning
Ask your team to set goals for themselves and how they plan to achieve, keep them up to date with the latest quality tools. Keep learning fun and innovative.
Take Your Quality to the Next Level
If your company is looking for an advanced manufacturing partner that is committed to the highest level of quality, contact Keller Technology Corporation. We’re ready to take on your next equipment build, fabrication task or complex manufacturing project. Contact us directly to see how we can partner together to improve your manufacturing quality.