“Cleanroom Assembly” for Keller Technology means the precision assembly of sophisticated electromechanical assemblies and equipment in a controlled environment: not the construction of the cleanroom itself. We will, however, touch briefly on the build and commission of our latest clean room below.
Typical industries that require cleanroom assembly include semiconductor, medical equipment, particle accelerator and beamline components, and systems requiring cleanliness for ultra-high vacuum operation.
What is a Cleanroom?
A clean room is an enclosed physical space containing a controlled environment that limits the concentration of airborne particles to a defined standard. It is constructed to minimize the ability of particulates to enter, proliferate, or exist within the space, with a HEPA filtration system serving as the base technology. Other factors that also controlled within the cleanroom include temperature, humidity, air flow, and pressure. Keller maintains four controlled environment cleanrooms at its various manufacturing facilities to the ISO 7 standard, with the ability to achieve ISO 5 below our laminar flow hoods.
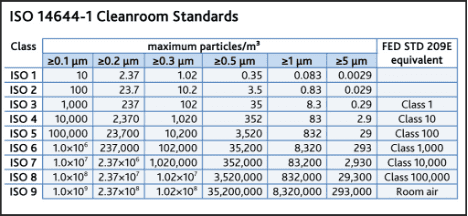
Building & Commissioning a Cleanroom
Both rigid wall and soft wall cleanrooms are utilized at Keller Technology. Our most recent addition is a 648 SF soft wall cleanroom constructed by Modular Cleanrooms. The decision to build a soft wall clean room was influenced by the flexibility of its design which allows it to be moved, reconfigured, and expanded to meet the needs of our customers. Following agreement upon purpose, design and performance characteristics, an order was placed with the manufacturer for the new clean room.
The validation process is typically segregated into three distinct phases:
- Phase 1 tests whether performance parameters are achieved in an empty room.
- Phase 2 adds equipment to the room for “at rest” testing.
- Phase 3 includes the addition of materials and workers performing their required activities.
At each phase the testing includes airborne particle counts, airflow volume and velocity, filter leak, humidity, temperature, pressurization, recovery, and smoke testing.
Following successful completion of testing in all phases the clean room is certified and can be used according to its intended purpose.
Monitoring & Maintaining the Cleanroom
Certification of the clean room does not mean that testing is over with. In fact, continuous monitoring of the air quality is necessary to maintain environmental control of the clean room while customer projects are integrated. Keller has written, stringent SOPs that detail the daily, weekly, monthly, etc. activities required to ensure the integrity of a clean room.
Real-time air quality measurements are conducted automatically within each controlled environment room and include temperature, relative humidity, and particle count. Should an alert threshold be reached the device immediately alerts staff, both visually and audibly, to implement recovery procedures.
Maintenance of the clean room also requires contamination prevention and cleaning processes to be documented and vigorously followed.
Cleaning the Cleanroom
Routine tasks for maintaining the particle count within the controlled environment include vacuuming with an approved vacuum, wet mop of floors with Isopropanol solution, trash and packaging material removal, wipe down of room frames, all work surfaces, benches and stools. Cleaning activities are recorded in the Cleaning Log. Periodic checks are conducted on the HEPA filters and they are replaced as necessary.
Procedures for People
Chief among the protocols for maintaining the integrity of the clean room is the Gowning Procedure for entry into the controlled environment. Keller has a SOP and slide deck that must be reviewed, understood, and followed strictly by everyone prior to entering the Gowning Room. Once inside, a very specific sequence of actions (gown, gloves, booties, hair and face net) is completed in the Gowning Room before entrance to the clean room is permitted.
Procedures for Materials
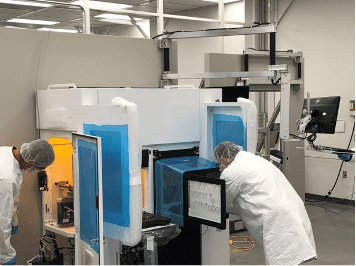
Tools, equipment, and materials for projects must also gain entry to the clean room without jeopardizing the sterile environment from cross contamination. Similar in function to the Gowning Room, an Ante Room is utilized to stage and clean physical objects intended for the controlled environment. Dedicated clean room material handling equipment is used to transfer thoroughly cleaned WIP into the clean room.
An extensive list of materials that are strictly prohibited from gaining entry to the clean room is also documented and includes packing peanuts and paper bags, wood, tape, natural fiber cloth, food, cosmetics, etc.
Clean Room Assembly of Complex Assemblies and Equipment
Keller Technology specializes in the repeat build of sophisticated electromechanical assemblies, high-level assemblies, and turnkey equipment within our dedicated controlled environment areas for many different industries, such as nanotechnology and deposition.
If you are interested in outsourcing clean room assembly, we invite you to visit one of our facilities to learn how Keller can support every stage of your manufacturing process.