- The goal of Non-Destructive Testing (NDT) is to confirm structural integrity without damaging it.
- NDT technologies utilize mediums like sound waves, lasers, magnetic particles, x-rays, vibration, electrical current, radio waves, special liquids, and gasses.
- There are many highly sophisticated NDT methods to verify the
integrity of a component, stock material, or system.
Choosing the right testing method is critical to evaluating the integrity of a component in an efficient and effective manner. Two options of testing for integrity of a component, stock material, or system are Non-Destructive Testing (NDT) and Destructive Testing. The goal of NDT is to confirm the structural integrity, conformance or functionality of a manufactured component or assembly, without damaging it. This allows the part to be used as intended after testing is completed, which in return saves you resources. Conversely, destructive testing damages a sacrificial part sample and is done as part of a statistical quality control program.
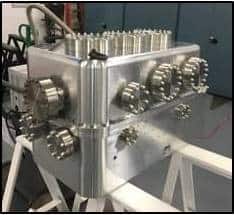
The names of NDT methods are often derived from the type of penetrating medium used or the scientific equipment needed to perform them. Modern NDT technologies utilize many different mediums, including sound waves, lasers, magnetic particles, x-rays, vibration, electrical current, radio waves, special liquids, and gasses. At Keller Technology Corporation (KTC), we utilize many different NDT processes. The type of tests used, and when we use them, depends on the engineering and manufacturing requirements of the particular part or assembly we are making. Three of the most common tests, that are used almost every day at KTC, are briefly described below.
- Visual Testing (VT) – The most frequently used NDT inspection process at KTC. As the name implies, this process utilizes the visual observations of trained machinists, fabricators, toolmakers, engineers, and inspection personnel. To enhance the observation process, it is common for the inspector to utilize special lighting, optical magnification, mirrors and borescopes to inspect assemblies, surfaces, and welding zones for cracks, corrosion, damage, or misalignments.
- Leak Testing (LT) – This NDT is typically used to verify that a pneumatic component assembly, ASME code pressure vessel or vacuum chamber is airtight within the defined parameters. There are four main types of leak tests:
- Bubble leak testing – Generally, this test uses compressed air, a tank of water, or a soapy solution to form air bubbles at a leaking area of the assembly. The bubbles are then noted by the inspector as part of a visual testing process.
- Halogen Diode testing – The Halogen Diode testing also utilizes a pressurized system of air and a halogen-based tracer gas. After a set period of time, a halogen gas “sniffer” instrument is used to detect and locate the presence of any leaks.
- Pressure Change testing – This utilizes a “closed system” where the part is filled with air. A change in air pressure or airflow is detected by a sensitive leak test instrument over a defined period of time.
- Mass Spectrometer Leak testing – This form of testing is a very sensitive detection process that can accurately detect extremely small leaks. The test can be set up a number of ways depending on the size and shape of the part under testing. In all cases, the detection of helium gas molecules by the test instrumentation determines the presence and size of the leak present.
- Liquid Penetrant Testing (PT) – The basic principle of PT is that when a highly fluid penetrating liquid is applied to the surface, a part of it will penetrate into tiny fissures and voids will open to the surface. After waiting a prescribed dwell time, the inspector removes excess penetrant from the surface and applies a developer material. The trapped penetrating liquid will flow back out to the surface, contact the developer, and become humanly visible by standard or fluorescent light. This type of test will detect cracks that do not pass all the ways through the wall and become leaks detectable via leak testing. However, Liquid Penetrant testing does not work well with porous surfaces. It is imperative that the surface under test is very clean prior to inspection.
There are many more, highly sophisticated, non-destructive testing methods used to verify the integrity of a component, stock material, or system. At KTC, we take pride in knowing that our products meet or exceed our customers’ requirements for quality and workmanship. Contact KTC today for more information about our NDT capabilities and part inspection experience.