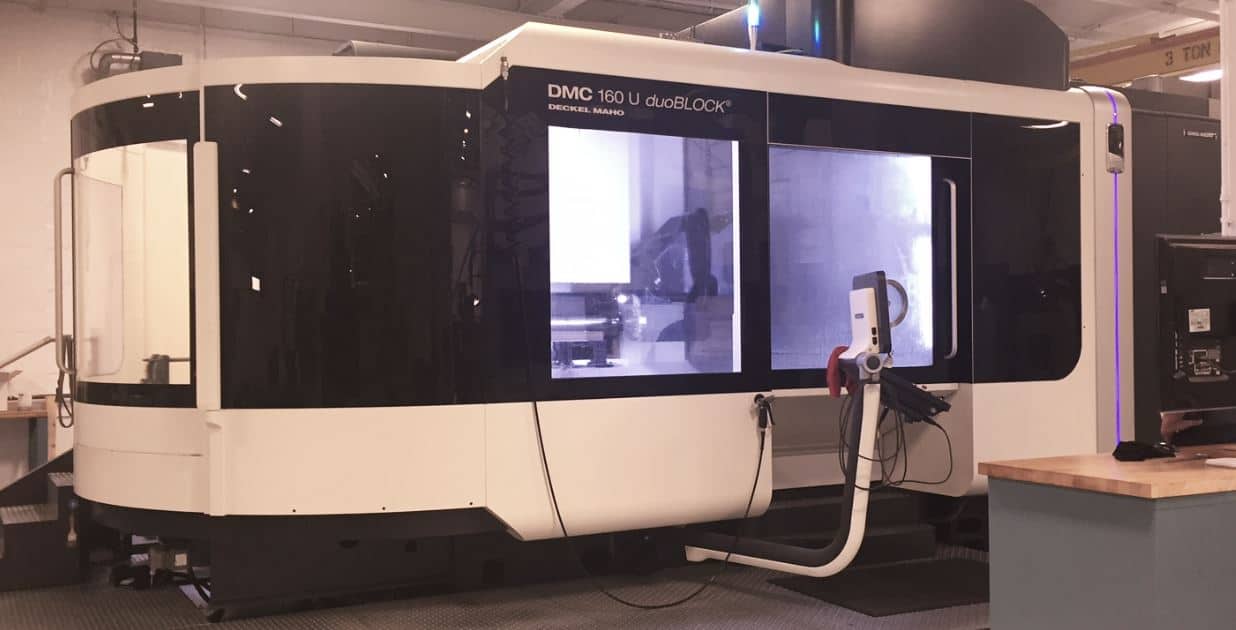
- DMG Mori Seki DMC 160 U five-axis universal mill features 66” x 55” table travel, 43” of vertical travel, a 12,000 rpm spindle, and a rotary pallet.
- Dual pallet allows for reduced spindle downtime and continued machining, while simultaneously setting up the next part for machining.
- 240-position automatic tool changer helps reduce spindle downtime with large-capacity tool loading and reduced setup times.
Constant pressure to reduce costs is a stark reality for modern manufacturing companies. Keller Technology Corporation’s customers benefit from our culture of continual improvement, a cutting-edge mindset and drive to help them attain their financial goals. One way we do this is by consistent investment in leading-edge technology and equipment. We recently purchased a DMG Mori Seki DMC 160 U five-axis universal mill. This machine tool features 66” x 55” table travel, 43” of vertical travel, a 12,000 rpm spindle, and a rotary pallet.
The capabilities of the DMC 160 U has allowed us to realize significant time reductions on the machining of legacy parts formerly done on other machine tools. Depending on the type of part, these savings can range from 20-50%. Other benefits include:
- A dual pallet that allows for reduced spindle downtime and continued machining while simultaneously setting up the next part for machining.
- A 240 position automatic tool changer that has helped reduce spindle downtime with large-capacity tool loading and reduced setup times.
- The flexibility to move between jobs quickly, as the variety of our works requires us to be extremely nimble in this regard.
To compliment and leverage the technical capabilities of this machine, we have implemented a cell-based setup, which enables Keller Technology’s five-axis machine to run “lights-out” and unmanned machining scenarios. This combination of ingenuity and technology to drive productivity is a necessity in today’s competitive environment. Coupled with our Lincoln robotic welding system, we are able to produce complex parts such as vacuum chambers, load locks, flexures, frames, and other complex welded precision fabrications with geometries requiring five-sided access.
As a contract manufacturer of complex machinery and equipment, we recognize that much of the cost of what we build tends to be in large machined and fabricated components. We continually challenge ourselves to improve and realize greater efficiencies, whether in technology, process improvement, or investment in people. Our latest investment in five-axis machining capability has enabled us to continue to aggressively attack costs in a very impactful way for our customers.
Have a project requiring our level of five-axis machining capabilities? Send us a message today to find out how Keller Technology can assist you.